工作機械スピンドルは機械加工の中核部品であり、加工精度、効率、製品品質に直接影響します。スピンドルの主な機能は、工具やワークピースを回転駆動して、切断、研削、穴あけなどのさまざまな加工操作を実行することです。現代の工作機械の主軸は、さまざまな駆動方法や用途の要件に応じて、ベルトタイプ、ダイレクトドライブ、ギアタイプ、内蔵スピンドルに分類できます。これらのさまざまなタイプのスピンドルにはそれぞれ長所と短所があり、さまざまな加工条件やニーズに適しています。
主軸の種類とその特徴を理解することは、適切な工作機械を選択し、加工効率を向上させる上で非常に重要です。例えば、高精度な加工が必要な場合には剛性と精度の高い主軸を選択することで加工効果が大幅に向上し、重切削を行う場合には高トルクの主軸を選択することで安定性と効率性を確保することができます。各工作機械は設計コンセプトや動作原理が異なり、それに対応する保守コストや使用コストも大きく異なります。したがって、実際の加工ニーズと経済状況に基づいて適切なスピンドル タイプを選択することで、効果的にコストを管理し、製品の品質を向上させ、熾烈な市場競争での優位性を維持することができます。
次のコンテンツでは、ベルトタイプ主軸、ダイレクトドライブ主軸、ギアタイプ主軸、ビルトイン主軸の 4 種類の工作機械主軸を簡単に紹介し、それぞれの利点、欠点、および適用可能なシナリオを分析します。この情報を通じて、読者が工作機械主軸の特性をより包括的に理解し、工作機械を選択および使用する際に、より多くの情報に基づいた決定を下せるようにしたいと考えています。
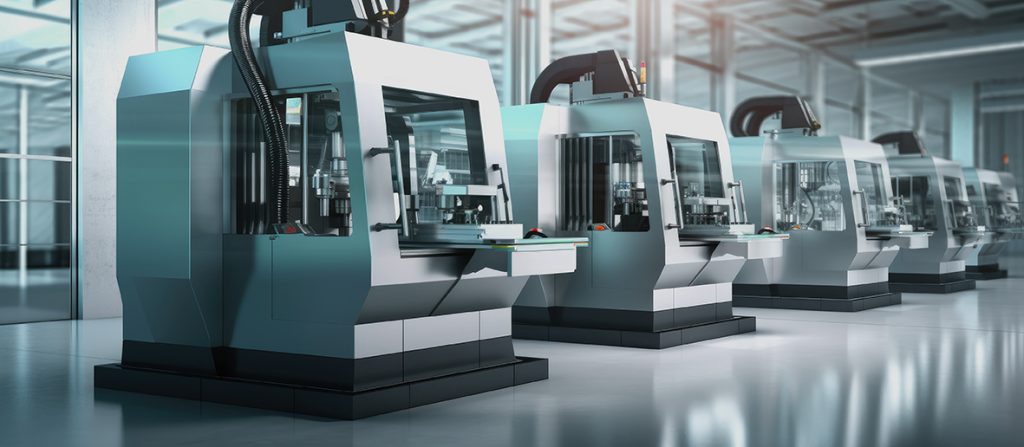
工作機械スピンドル構造の紹介
ベルトスピンドル
ベルト式スピンドルはモーターの動力をベルトを介してスピンドルに伝達するため、構造が簡単で低コストという利点があります。ベルトは機械振動の一部を吸収し、加工中の振動の影響を軽減します。ただし、ベルトの弾性により伝動効率が低く、主軸回転速度やトルクにある程度のロスが生じるため、高精度を必要としないワークの加工に適しています。
ベルトタイプのスピンドルにもいくつかの欠点があります。ベルトの弾性により動力伝達効率が低く、主軸速度やトルクが若干低下し、加工効率や精度に影響を与えます。ベルトは摩耗しやすいため定期的に交換する必要があり、メンテナンスコストが増加します。ベルトの弾性特性により伝達精度が高くないため、軽中量加工など高精度を必要としないワークの加工にはベルト式主軸の方が適しています。
ダイレクトスピンドル
直結主軸はモータを主軸に直接取り付けるため、中間の伝動部品が不要となり、動力伝達効率と精度が非常に高くなります。この設計により、非常に高い回転速度とトルク伝達精度が得られ、航空宇宙や精密金型の製造など、高い精度と速度が要求される加工用途に最適です。中間伝動部品がないため、運転時に発生する振動や騒音が低くなります。
この構造は、モーターとスピンドルの完璧な組み合わせを保証するために高精度の製造プロセスを必要とするため、製造コストが高くなります。高速動作では大量の熱が発生する傾向があるため、安定性を維持するには効率的な冷却システムが必要です。また、直結主軸は修理や部品交換が難しく、維持費が高くつきます。
ギヤードスピンドル
ギヤードスピンドルは、モーターの動力をギヤボックスを介して主軸に伝達するため、高トルクと安定した回転速度を実現し、自動車製造や造船産業などの重切削や大規模加工に適しています。ギアは動作中に摩耗して騒音や振動を発生し、加工品質に影響を与えるため、定期的な潤滑とメンテナンスが必要です。
しかし、運転中にギアが摩耗し、騒音や振動が発生し、加工品質に影響を及ぼします。ギアボックスには定期的な潤滑とメンテナンスが必要であり、運用コストが増加します。歯車式スピンドルは構造が比較的複雑で、製造やメンテナンスには専門的な技術サポートが必要であり、使用の難易度も高くなります。
ギア付きスピンドルは、重いワークピースや大量生産を処理する必要がある企業に適しています。メンテナンスコストは高くなりますが、その強力な耐荷重性と動作の安定性は、特定のアプリケーション分野ではかけがえのない利点をもたらします。
内蔵スピンドル
ビルトインスピンドルは、スピンドル内部にモーターを組み込んで一体構造とした設計です。ダイレクトマウントスピンドルの高精度とベルトタイプスピンドルの振動減衰特性を兼ね備えた設計で、高い剛性と精度を有し、ハイエンドの精密加工用途に適しています。この設計は、内部構造を完全に一致させるために精密な製造プロセスと技術を必要とするため、製造コストが非常に高くなります。内部構造が複雑でメンテナンスや部品交換が難しく、技術者の要求も高いです。さらに、高速動作では多量の熱が発生するため、安定した動作を維持するには効率的な冷却システムが必要です。
内蔵スピンドルは、加工精度と安定性に対する非常に高い要件が求められる企業に適しています。初期投資やメンテナンスコストは高くなりますが、その優れた性能と高い安定性は、ハイエンド精密加工の分野ではなくてはならないものです。
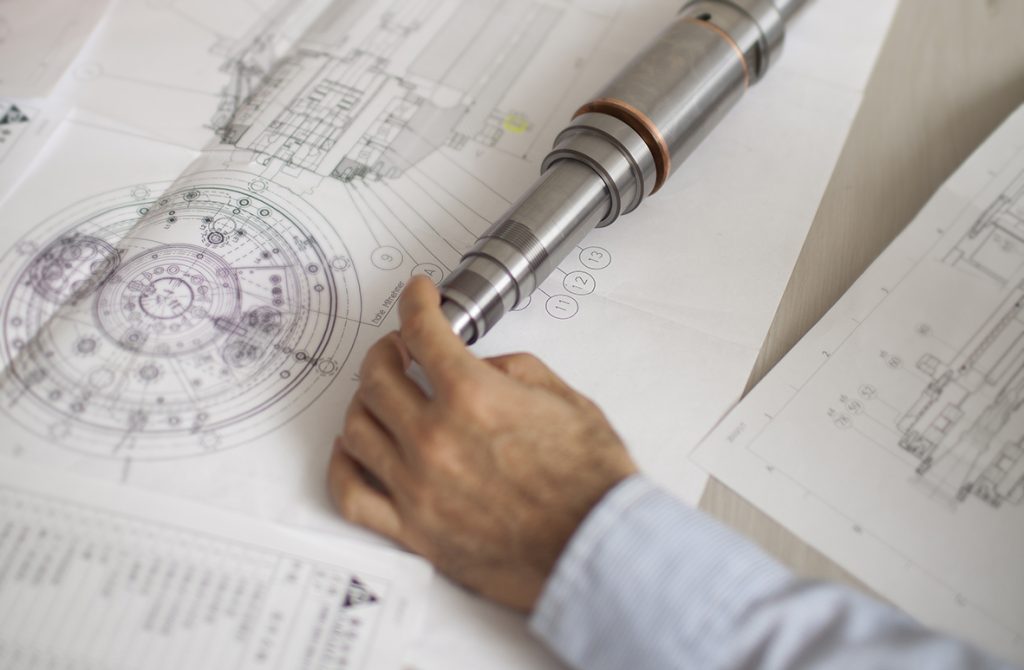
工作機械スピンドル剛性の比較
主軸の剛性は加工精度と安定性に影響を与える重要な要素の一つです。高剛性主軸により、重負荷切削時の安定性を維持し、加工時の変形や振動を低減し、加工品質を向上させます。スピンドルのタイプが異なると、剛性の点で異なる性能が得られます。
ベルトスピンドル :ベルトの弾性により剛性が比較的低く、軽・中量加工に適しています。
ダイレクトスピンドル :中間伝動部品の影響を受けず、モーターが直接主軸を駆動するため高剛性です。
ギヤードスピンドル :剛性が高く重切削に適していますが、定期的なギヤボックスのメンテナンスが必要です。
内蔵スピンドル :最高の剛性を有し、超高精度加工用途に適しています。
工作機械スピンドルメンテナンスの違い
スピンドルの修理とメンテナンスは、加工精度を確保し、寿命を延ばすために重要な部分です。スピンドルの種類が異なれば、修理のしやすさや修理費用も異なります。
ベルトスピンドル:メンテナンスは定期的にベルトを交換するだけで比較的簡単でコストも安価です。
ダイレクトスピンドル:修理や部品交換が難しく、維持費が高くつきます。
ギヤードスピンドル:歯車は定期的な注油とメンテナンスが必要で、構造が複雑でメンテナンスコストが高くなります。
内蔵スピンドル:内部構造が複雑でメンテナンスや部品交換が難しく、技術者の要求も高く、コストも高くなります。
要約する
加工会社にとって、適切な工作機械スピンドルの選択は非常に重要です。各スピンドル設計には、独自の利点、欠点、および用途の範囲があります。低コストの基礎加工に適したベルトタイプ主軸、高精度・高速加工ニーズに適した直結主軸、重切削に適したギヤタイプ主軸、ハイエンドの精密加工に優れた主軸です。さまざまなスピンドルの長所と短所を理解することは、ユーザーが工作機械を選択および使用する際に、より多くの情報に基づいた意思決定を行うのに役立ち、加工効率と製品品質を向上させることができます。
さらに、油圧スピンドル、空気静圧スピンドル、電磁スピンドルなど、他のタイプのスピンドル設計もあります。油圧スピンドルは油圧システムにより駆動され、剛性と安定性が高く、高負荷・高精度の加工に適しています。気力静圧スピンドルは、圧縮空気により形成される空気膜を利用して主軸を支持・駆動するため、非常に高い回転精度と低摩擦特性を有し、超精密加工に最適です。電磁スピンドルは電磁力により主軸を駆動・支持するため、無摩擦・高速・高精度の特性を持ち、超高精度加工用途に適しています。
科学技術の進歩に伴い、工作機械スピンドルの設計および製造技術は発展し続けており、将来的にはさまざまな加工ニーズを満たすために、より多くの新しいスピンドル設計が登場する可能性があります。加工効率と競争力の向上には、最新のスピンドル技術を理解して使いこなすことが不可欠です
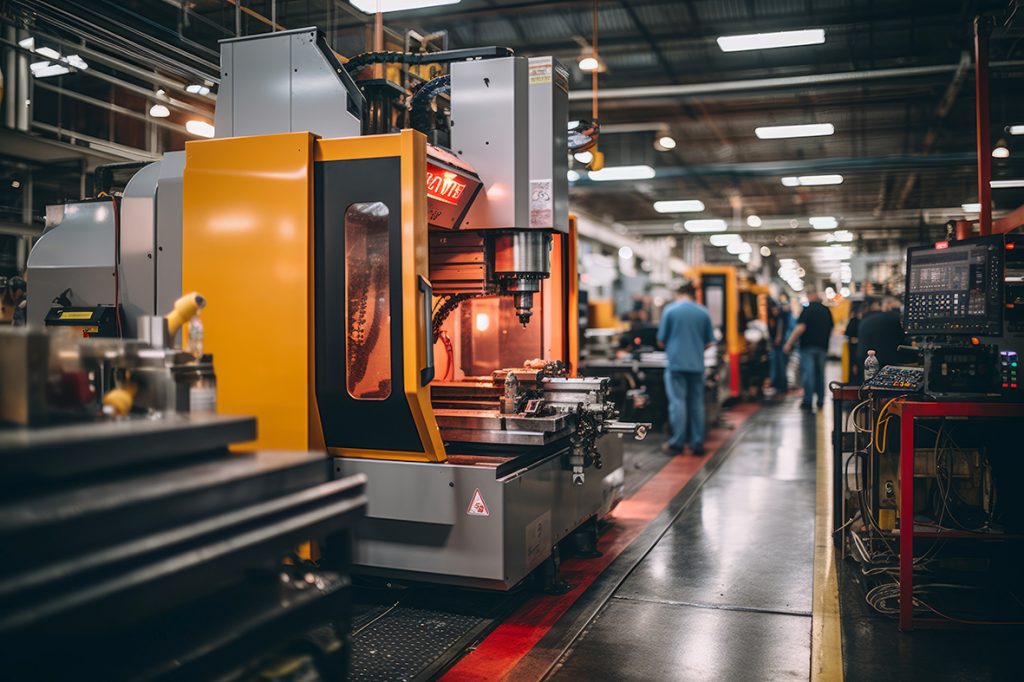
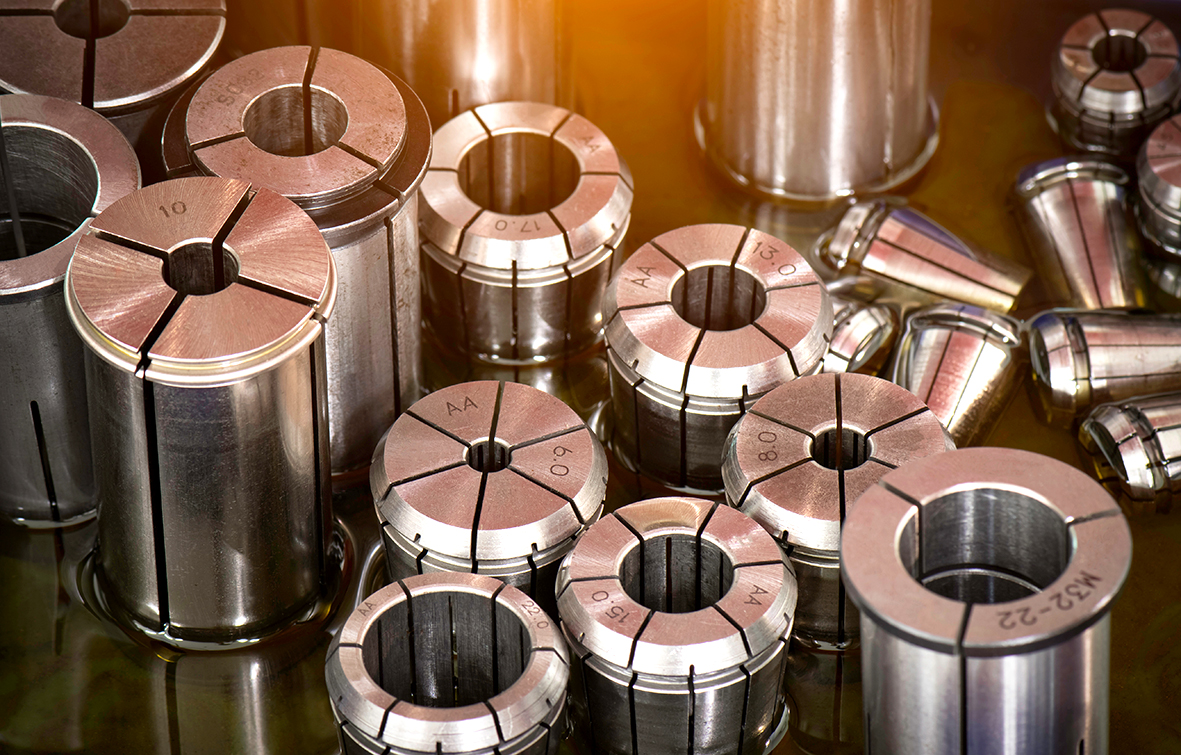
コレット ― CNCツーリングの隠れた主役
July 11, 2025
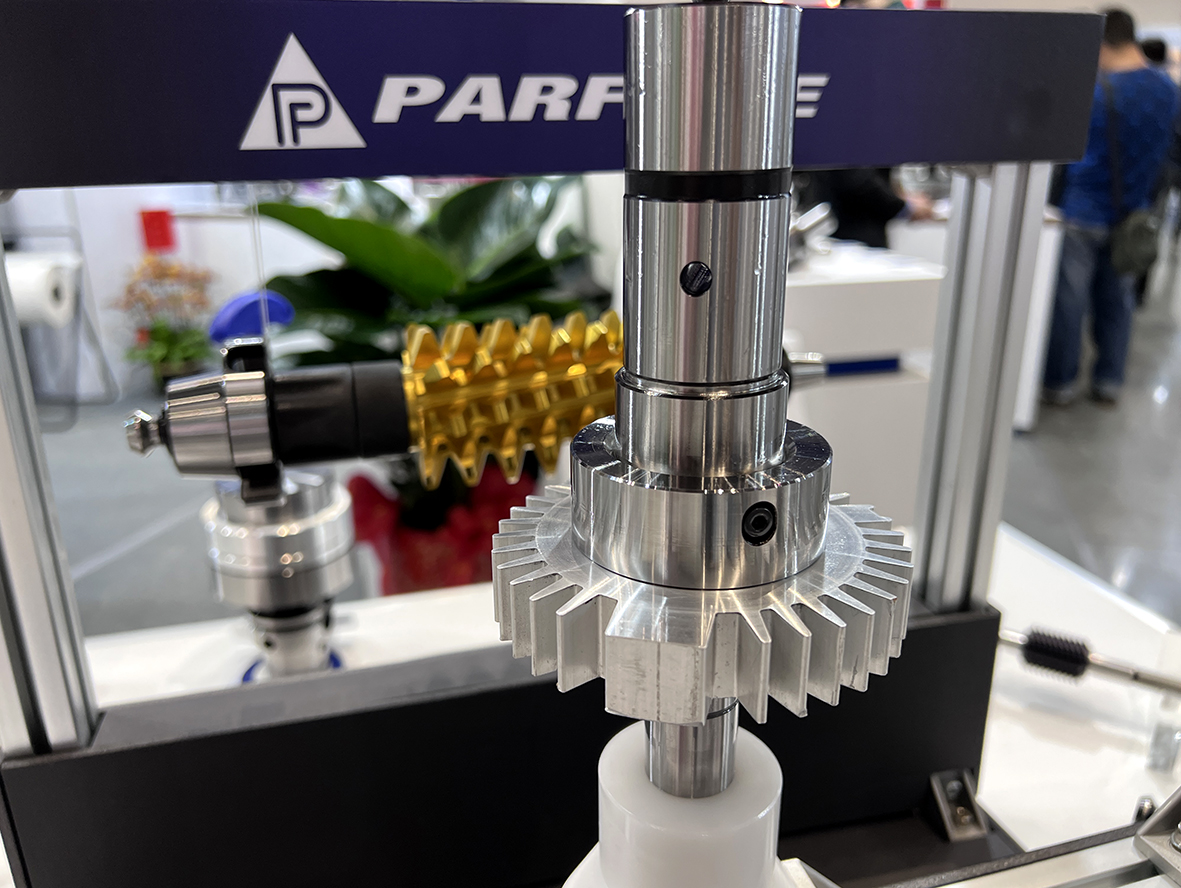
カスタマイズ対応・油圧式膨張マンドレル ― 先端製造業向けの高精度ワーク固定ソリューション
June 30, 2025
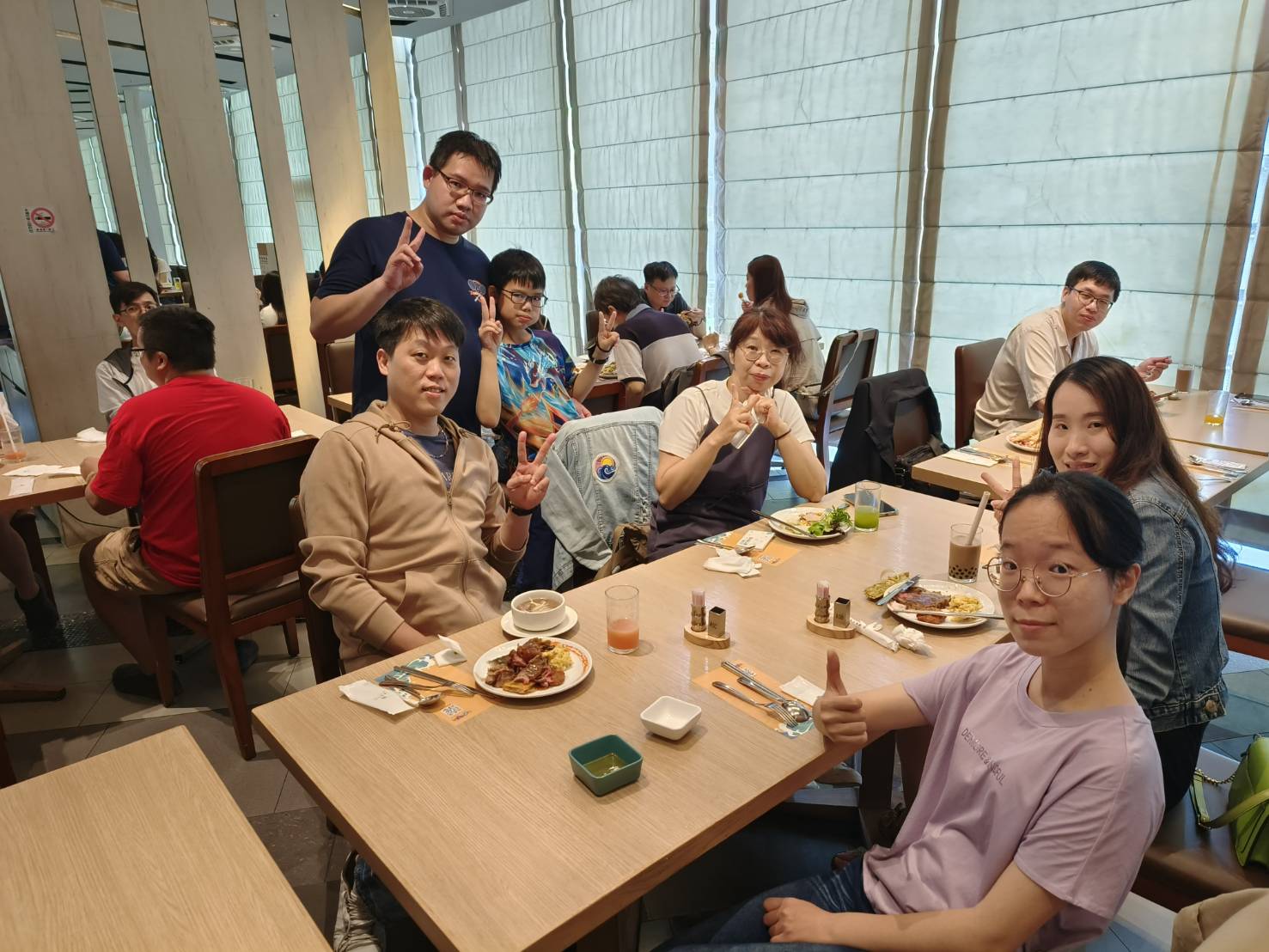
Parfaite企業 2025年社員懇親会|温かいひととき、共に過ごす時間
July 15, 2025
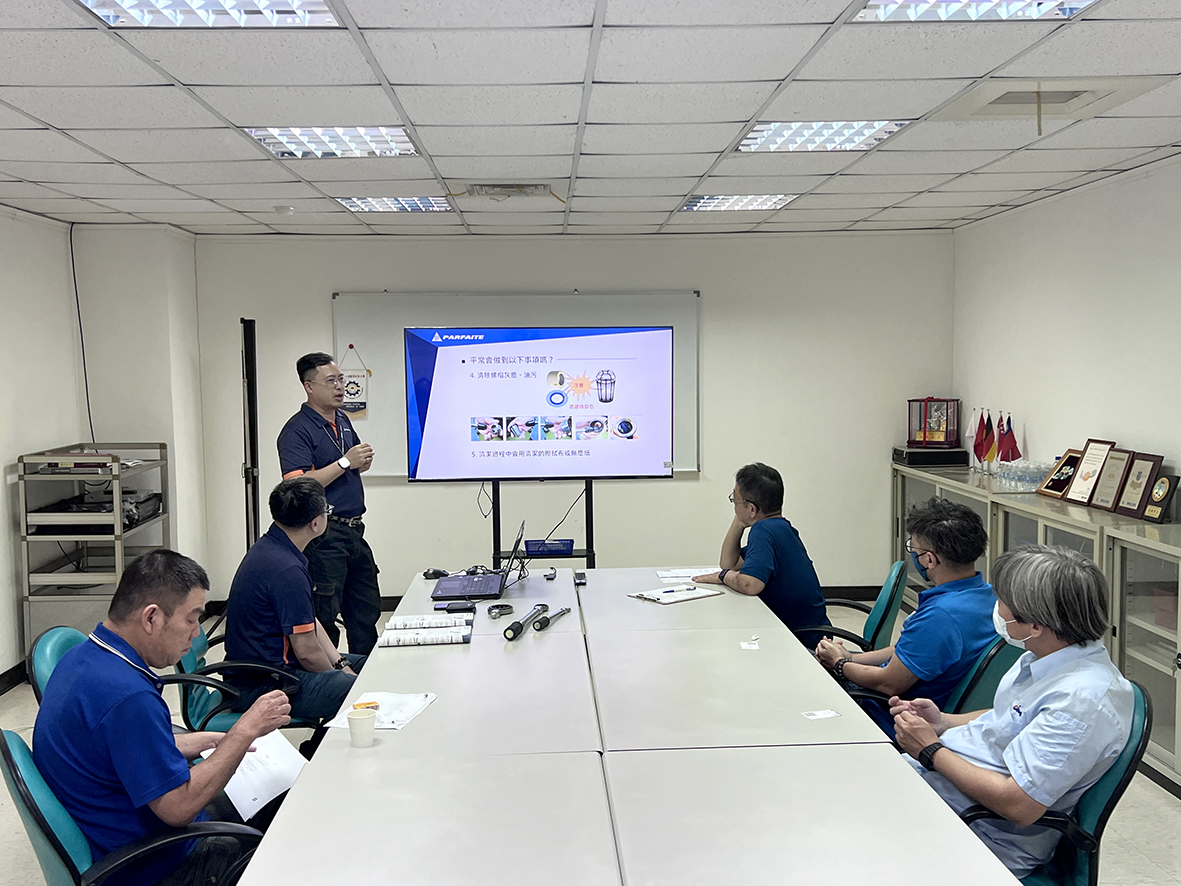
Parfaite、南部の精密加工工場にてツールホルダー保守の実践ノウハウを共有 — 高い評価を獲得
June 2, 2025