CNC 加工の世界では、「高精度」「高効率」「高安定性」が常に求められる三大要素です。一般的にツーリングシステムではツールホルダーに注目が集まりがちですが、その性能を最大限に引き出すために欠かせない部品があります ― それが「コレット(collet)」です。 コレットは、工具シャンクとホルダーをつなぐ重要な中間部品であり、その把握力(クランプ力)は加工精度、工具寿命、そして機械の安定性に大きく関わります。本記事では、コレットの基本構造から種類、選定ポイント、メンテナンス方法までをわかりやすく解説し、最適なツーリングシステム構築のヒント
コレットとは?精密加工を支える縁の下の力持ち
コレットは、外径にテーパー形状を持ち、内径は真円状の穴が空いた円筒形のバネ部品です。通常はコレットナット(またはキャップ)と組み合わせてツールホルダーに装着され、ナットを締めることでコレットが収縮し、工具シャンクを均等に強く把握します。 この構造により、高速回転中でも工具をしっかり固定でき、振れ精度が高く、再現性にも優れます。特に高速・高精度なフライス加工や穴あけ加工では、コレットは決して欠かすことのできない重要部品なのです。
代表的なコレットの種類と特徴:最も普及しているERシリーズ
ERコレットシリーズ ― CNC 加工における世界標準
1. ERコレットの起源と国際規格
ERコレットは1972年、スイスのRego-Fix社によって開発され、現在ではDIN 6499およびISO 15488の国際規格に準拠する、最も汎用的なコレットシステムとなりました。その優れた柔軟性と広範な把握範囲により、フライス・ドリル・タップ・彫刻など多用途に対応できるため、今日のCNC加工業界において最も普及しているコレット形式です。
2. 構造とクランプ原理
ERコレットは、一般的に8〜16本のスリット(弾性スロット)を持ち、軸方向に力がかかると、スリットが収縮し、均等な円周方向のクランプ力を発生させます。使用時は、まずナットの内側にある「溝」にコレットを装着し、ホルダーに取り付けてからナットを締めることで、コレットがテーパー穴に押し込まれて工具シャンクをしっかりと把握します。 主なメリット:
- 均一な360度の把握力(片当たりを防止)
- ±0.5mm の範囲でシャンク径の誤差に対応
- 工具交換が迅速で、段取り時間を短縮可能
3. 主なサイズとクランプ範囲(ER11~ER40)
コレット型式 | 最大把握径 (mm) | 推奨クランプ範囲 (mm) | 外径 (mm) | 全長 (mm) |
ER11 | 7.0 | 1~7 | 11.5 | 18 |
ER16 | 10.5 | 1~10 | 17 | 27.5 |
ER20 | 13.0 | 1~13 | 21 | 31.5 |
ER25 | 16.0 | 1~16 | 26 | 34 |
ER32 | 20.0 | 2~20 | 33 | 40 |
ER40 | 26.0 | 3~26 | 41 | 46 |
それぞれのサイズに対応するセットを揃えることで、多様な工具シャンク径に柔軟に対応できます。
4. ERコレットの主要特長
· 高精度:振れ精度は最大 0.002~0.006mm(仕様により異なる)
· 広い把握範囲:1つのコレットで±0.5mm対応
· モジュラーシステム:ナット・ホルダー・延長ホルダーとの高い互換性
· 高い安定性:25,000rpm 以上の高速回転にも対応し、振動や加工誤差を抑制
· メンテナンス性:構造がシンプルで交換も容易、長寿命
5. 適用分野
- フライス加工:粗加工から仕上げまで対応
- 穴あけ加工:ドリルの振れ抑制に最適
- タップ加工:逆回転防止装置と組み合わせで高精度タップが可能
- 彫刻加工:ER8・ER11は金型や3C製品の精密彫刻に最適
- ATC(自動工具交換):機械自動化にも最適な設計
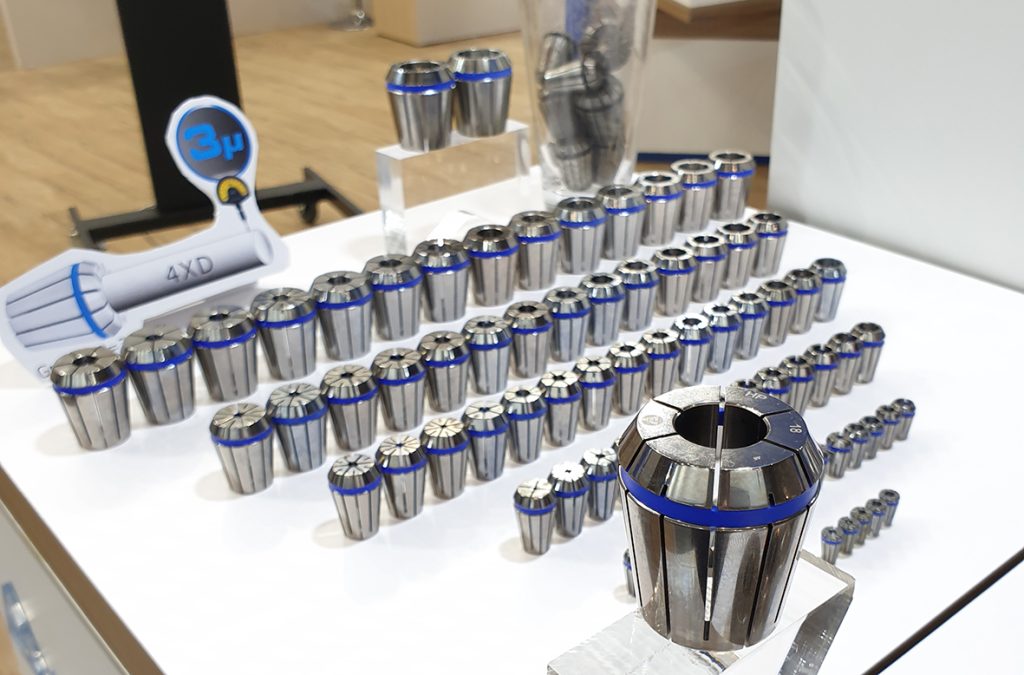
TGコレット:トルクが必要な重切削向け。高い保持力だがサイズが大きく、柔軟性は劣る。
DAコレット(ダブルアングル):古いタイプ。安価だが精度と安定性に欠け、現在では徐々に廃れている。
OZコレット:六角形外形で把握力が強く、木工や自動彫刻機などで多用される。
オートロックコレット:ネジ付きシャンク専用で、挿入と同時に自動ロックされる。量産ライン向き。
コレットとホルダー ― 精度を決めるツーリングシステム
BT30、BT40、HSK63、ISO40、CAT40などのツールホルダーは、コレットやナットとセットで使用します。特にERコレットは汎用性が高く、多くのホルダーに対応しています。適切なコレットとナットを使えば、工具交換の自由度が高まり、作業コストの削減にも貢献します。 ただし、不適切な組み合わせやトルク不足は、振れ増加・工具抜け・加工不良といった重大なリスクにつながるため注意が必要です。
高品質コレットを選ぶ理由
高精度なコレットは、工具の振れを大幅に減らし、加工面の仕上がりや工具寿命を向上させます。また、安定した把握力は機械のバランスにも貢献し、生産性全体を高める効果があります。一方で、安価なコレットや寿命を過ぎたコレットは、金属疲労や変形により保持力が低下し、加工精度や機械自体の故障につながる可能性があります。 だからこそ、厳しい公差・精密研削・適切な熱処理を施した高品質コレットの選定が不可欠なのです。
定期メンテナンスと交換が精密加工の第一歩
コレットとナットは工具交換ごとに清掃し、切粉や油分をエアブローと乾拭きで除去してください。長期間使用すると、金属疲労により弾性や把握力が低下し、偏ったクランプ力につながります。 標準的な使用頻度では2〜3ヶ月ごとの交換が推奨されますが、大量生産ラインではそれ以上の頻度で点検・交換が必要です。ナットおよびホルダーとの接触面の摩耗も定期的に確認してください。
最適なコレットで、加工品質をさらに一歩前へ
コレットは小さな部品ながら、ツーリングシステム全体の精度と安定性に大きく影響を与える存在です。高品質かつ用途に合ったコレットを選定し、正しい使用・定期交換を行うことで、ツールホルダーの性能を最大限に引き出せます。 PARFAITE(普慧)では、高精度・高剛性を誇るコレットおよびツーリングソリューションをご提供しています。金属加工・穴あけ・金型製作・自動生産など、あらゆる加工現場において、最適なホルダーとコレットの組み合わせで貴社の生産性を次のレベルへと導きます。
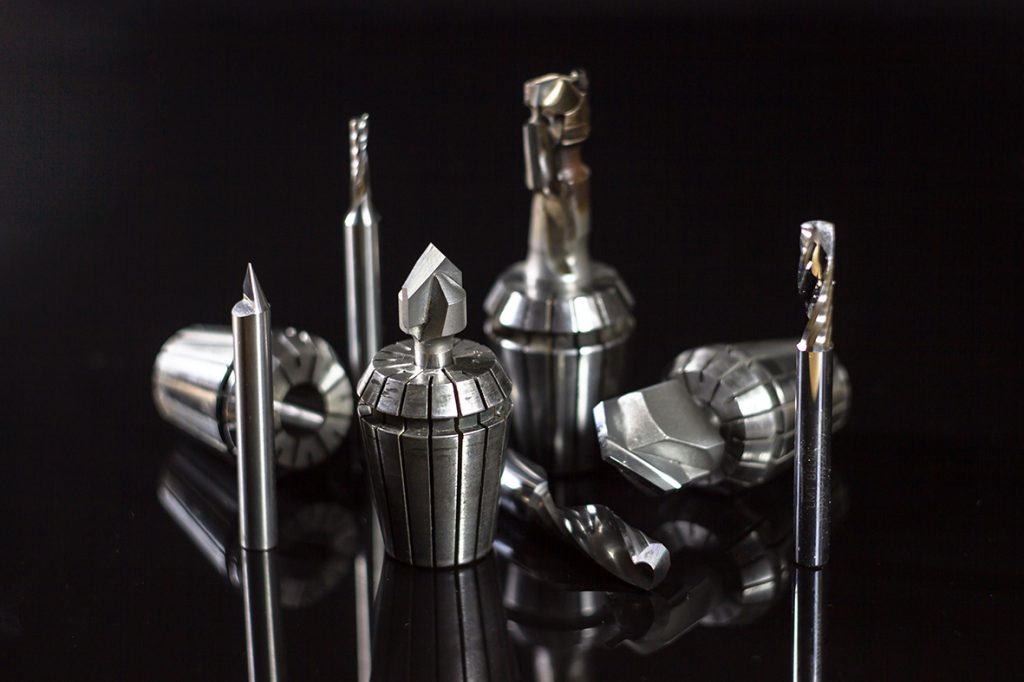
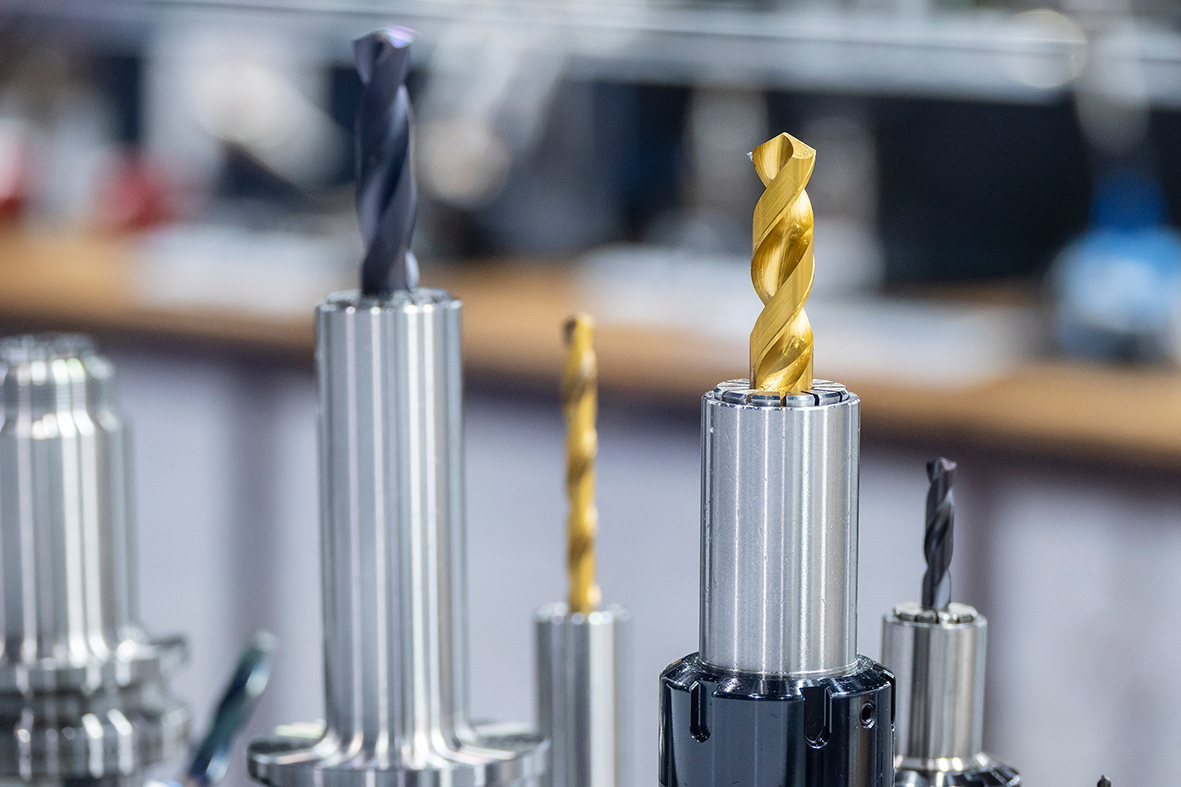
ドリルの種類と応用完全ガイド:適切な工具選択でCNC加工効率を向上
August 18, 2025
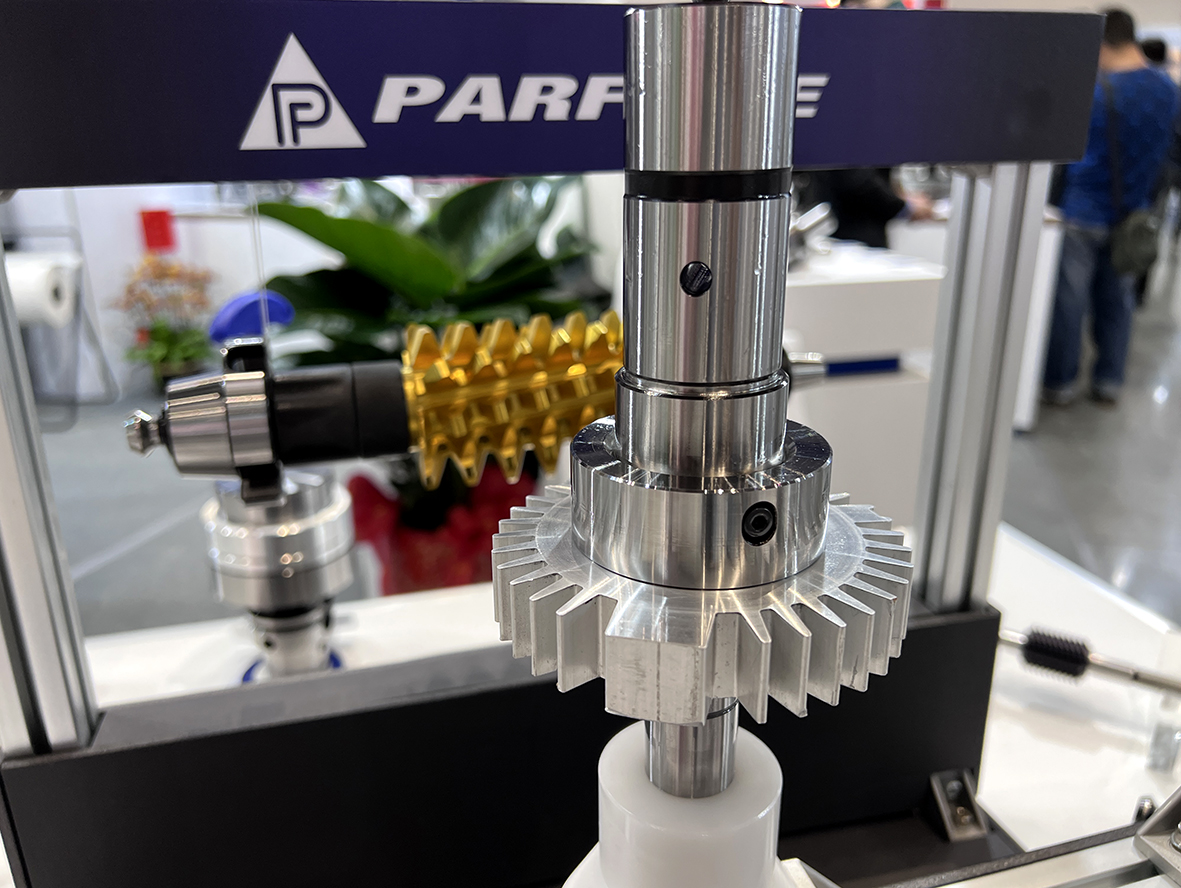
カスタマイズ対応・油圧式膨張マンドレル ― 先端製造業向けの高精度ワーク固定ソリューション
June 30, 2025
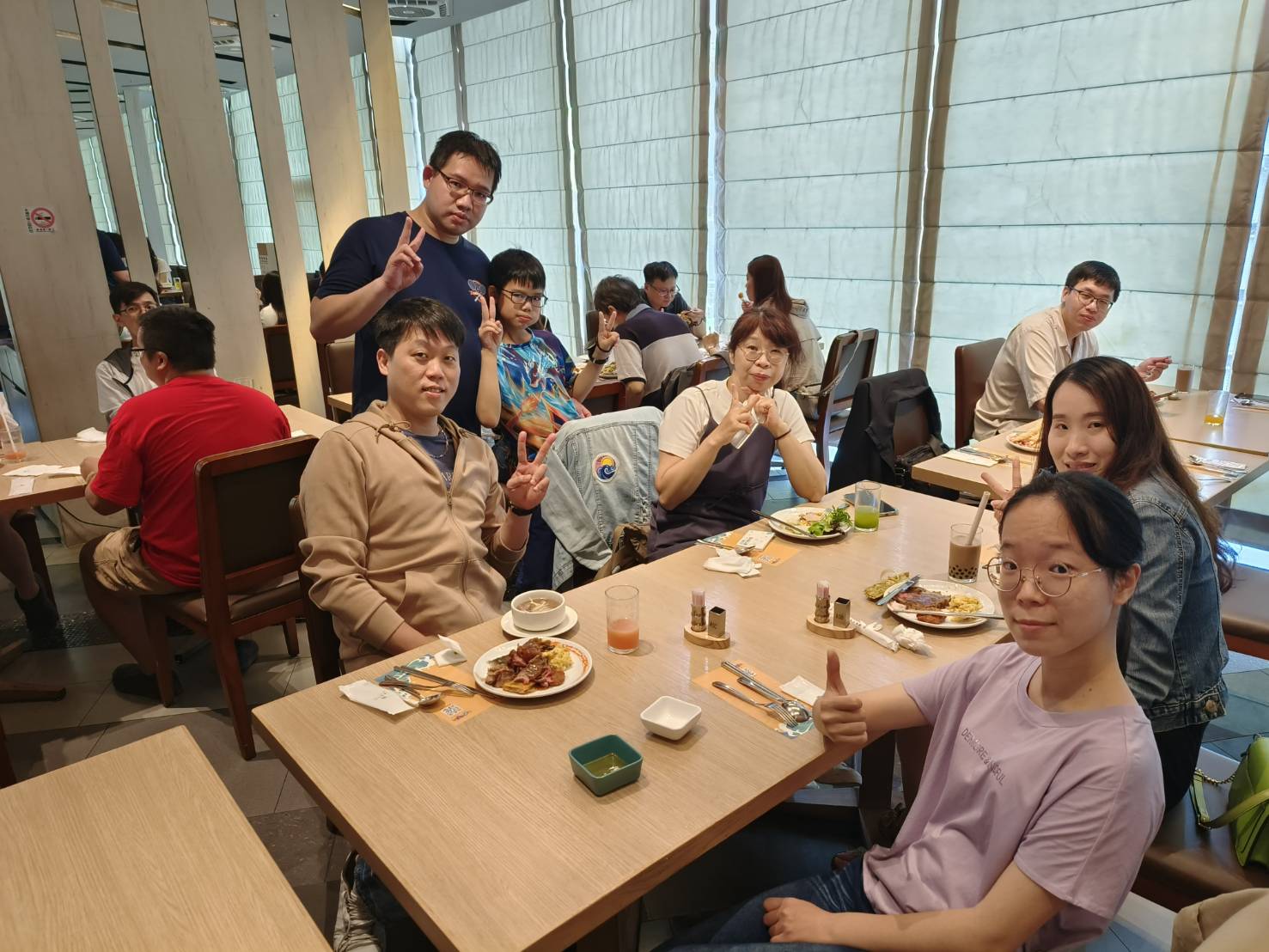
Parfaite企業 2025年社員懇親会|温かいひととき、共に過ごす時間
July 15, 2025
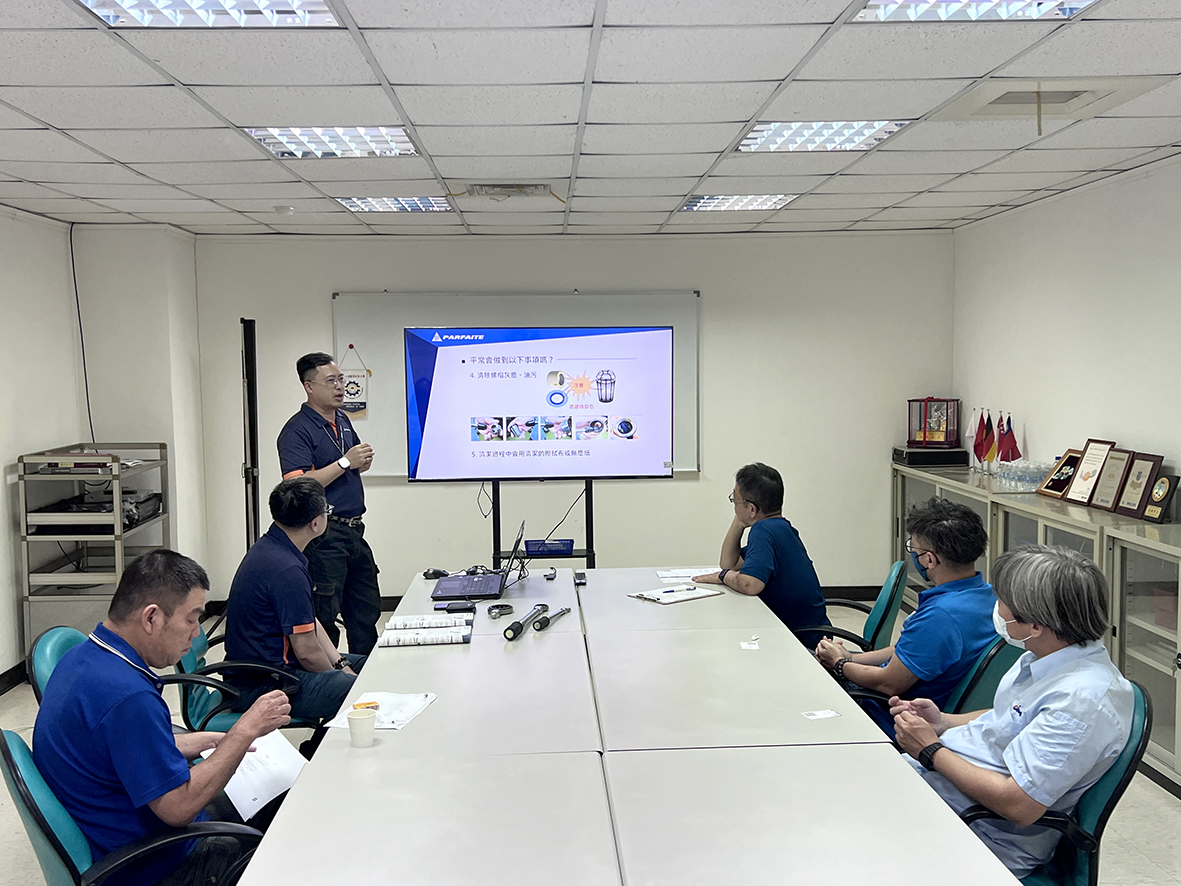
Parfaite、南部の精密加工工場にてツールホルダー保守の実践ノウハウを共有 — 高い評価を獲得
June 2, 2025