A brief discussion on precision CNC tool handles (tool holders)?
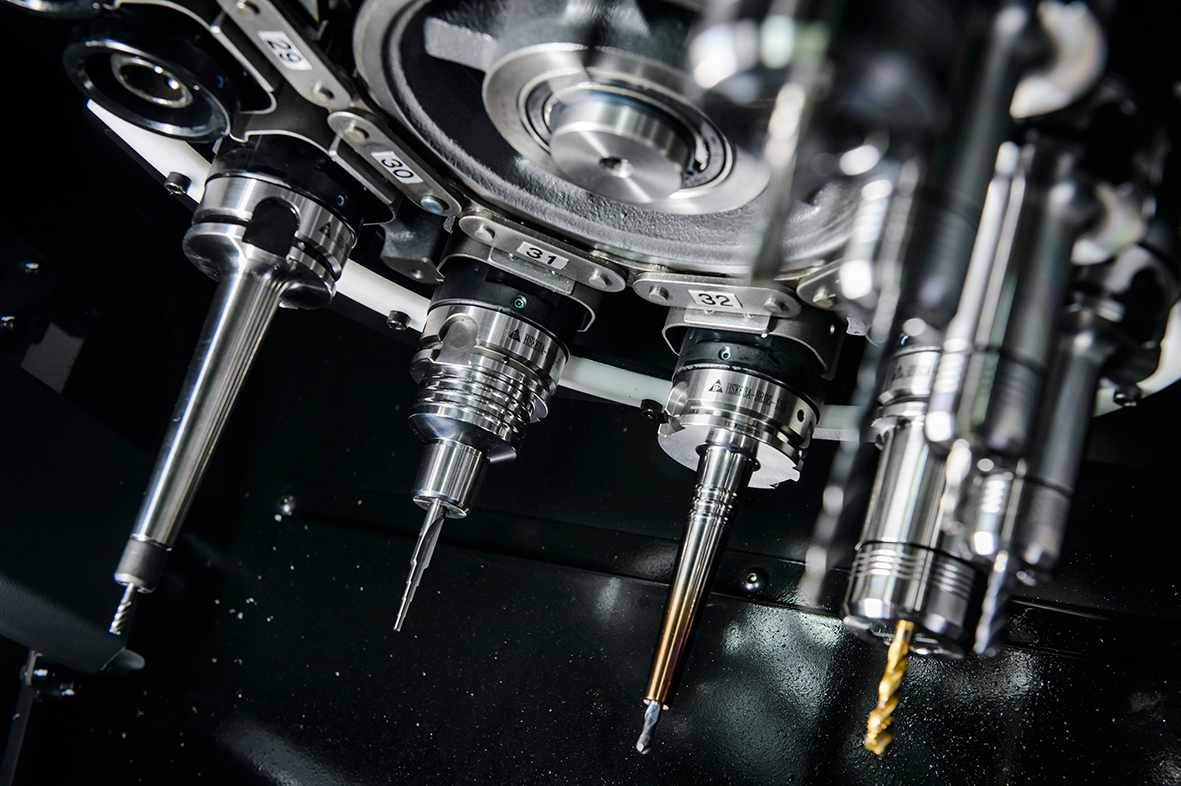
In modern manufacturing, CNC machine tools have become the main equipment for processing and manufacturing, and CNC tool holders (also known as tool holders) are an indispensable key component in CNC machine tools. Its main function is to hold the tool and transmit power to the tool to ensure accuracy and stability during the machining process. For machine tool manufacturers, the selection and application of CNC tool holders directly affects processing efficiency, product quality and equipment performance. Through the following functions, types, design features, application value and its role in machine tools, we will have a preliminary understanding of CNC tool holders.
Core functions of CNC tool holders
The primary function of the CNC tool holder is to hold the tool firmly and ensure that the tool remains stable during the machining process. It accurately transmits the power of the spindle to the tool through a high-precision clamping structure to realize cutting, drilling, milling and other processing operations. In addition, CNC tool holders also need to withstand huge cutting forces and vibrations during machining, so their design must have high rigidity and durability. For machine tool operators, choosing high-performance tool holders can significantly improve processing efficiency, reduce scrap rates and extend equipment life.
Types and applications of CNC tool holders
According to different processing requirements and machine tool types, CNC tool holders are divided into shank types, including BT type, HSK type, CAPTO type, etc. BT type tool holder is suitable for general machining centers and has good stability; HSK type tool holder is famous for its high speed and high precision and is widely used in the mold and aerospace fields; CAPTO type tool holder (the structure of the handle is not conical Shaped instead of a triangular cone), it is known for its high rigidity and quick tool change function. However, it should be noted that common tool holders in the existing market are not compatible, and self-locking problems may occur when using handles other than this system; The clamping end classification includes high-precision hydraulic tool holders, heat shrink tool holders or HER collet-type high-speed tool holders, as well as side-fixed tool holders for roughing and milling, powerful milling tool holders, and ER chuck-type tool holders. It is mostly used in processing scenarios such as drilling and tapping. It has a face milling cutter holder; a special tool holder for surface milling cutterhead, suitable for surface milling processing. Understanding the characteristics and application scenarios of different tool holders is an important step for machine tool manufacturers to improve their processing capabilities.
CNC tool handle design features
The design of CNC tool holders requires a balance of rigidity, precision and durability. High-quality tool holders are usually made of high-strength alloy steel and undergo precision machining and heat treatment to ensure their stability and life under high load. In addition, the dynamic balance performance of the tool holder is particularly important for high-speed machining, which can effectively reduce vibration and eccentricity and improve the quality of the machined surface. Modern tool holders also incorporate a modular design, which can be quickly assembled and replaced according to different needs, greatly improving processing efficiency.
The role of CNC tool handles in machine tools
The role of the CNC tool handle in the machine tool is not only to connect the spindle and the tool, but also a key link in achieving high-precision machining. It not only affects the machining accuracy, but also determines the service life of the tool and the stability of the machine tool. For machine tool manufacturers, high-quality tool holders can not only improve the performance of the equipment, but also reduce the frequency of equipment maintenance and tool wear, and reduce overall production costs. Therefore, CNC tool holders are one of the core elements for improving machine tool performance.
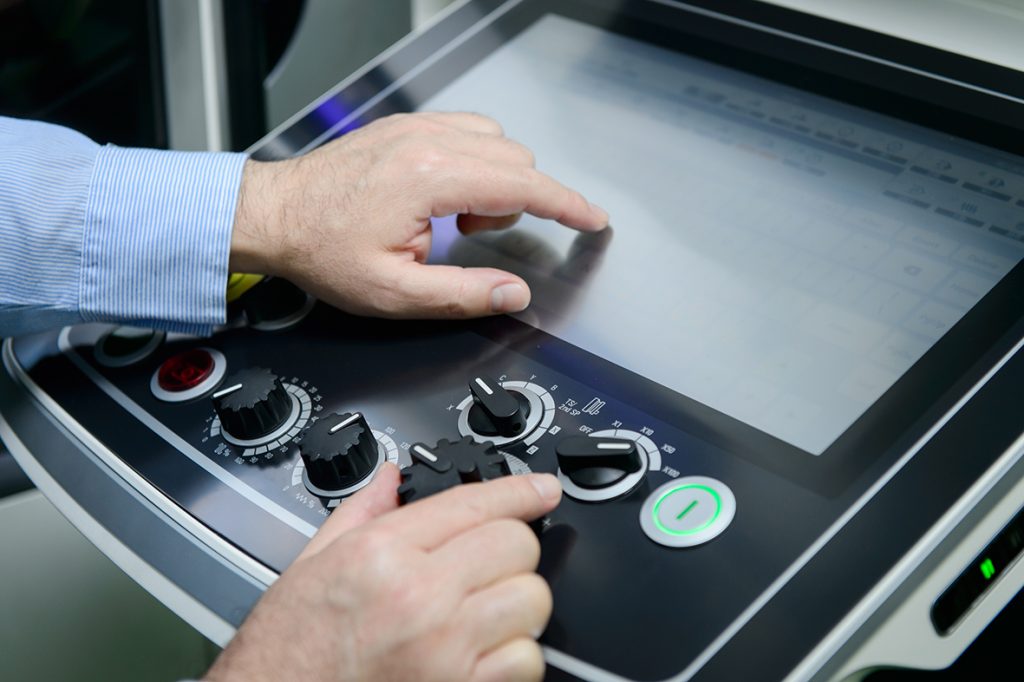
Smart knife handle-future development trend
As the manufacturing industry develops towards high precision and automation, the design and application of CNC tool holders are also constantly innovating. For example, smart tool handles combined with Internet of Things technology can monitor processing status and data in real time, improving production management efficiency. In addition, the application of lightweight and composite materials enables the tool holder to adapt to higher speed and more precise processing requirements. In the future, CNC tool holders will achieve more breakthroughs in performance, intelligence and environmental protection, bringing more business opportunities to machine tool manufacturers.
As an important part of CNC machine tools, CNC tool holders play an indispensable role in the machining process. From clamping the tool, transmitting power to improving processing accuracy and stability, the performance of the tool holder directly affects the overall performance of the machine tool. For machine tool manufacturers, choosing the appropriate tool holder and mastering its application characteristics are the keys to improving processing efficiency and product quality. In the future, with the advancement of technology and the diversification of needs, CNC tool holders will play a greater role in the manufacturing industry and help industrial upgrading and development.