What is a face milling cutter? What is a face milling cutter handle?
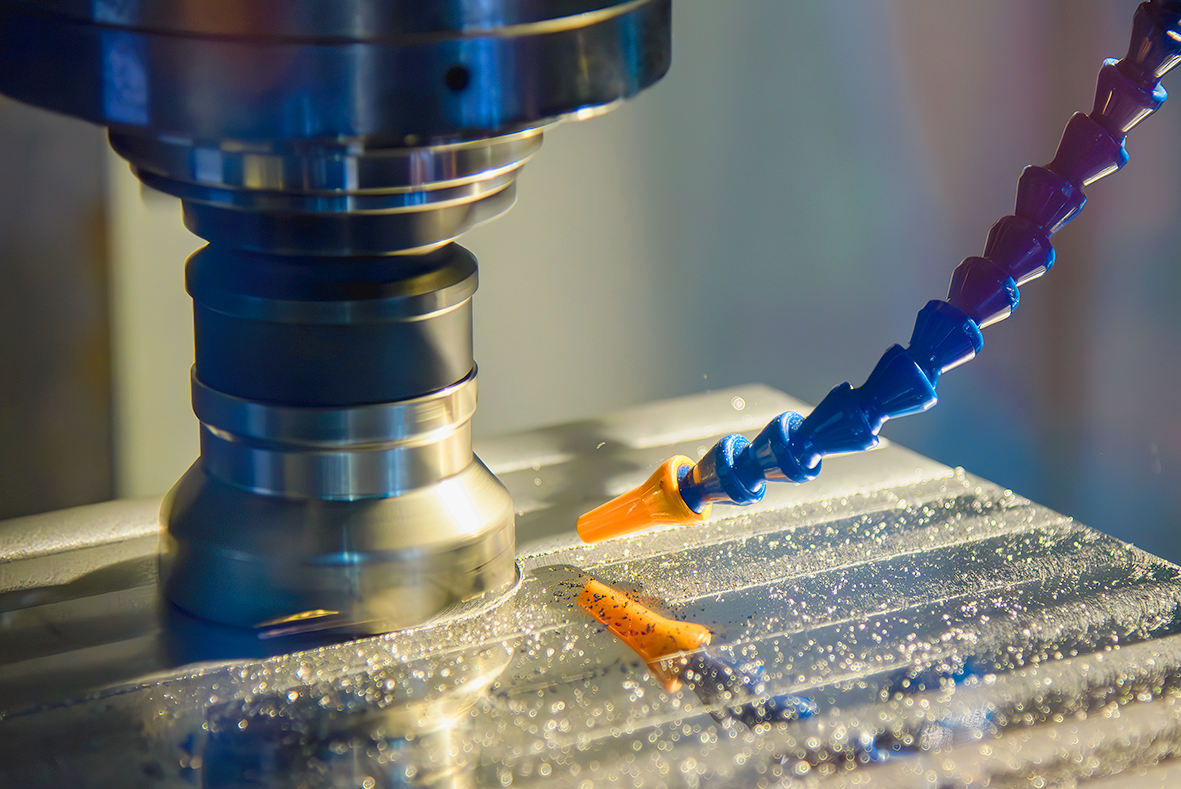
A face milling cutter is a tool used to machine the flat surface of a workpiece. It usually consists of a tool body and replaceable blades. It removes the metal surface layer by layer through high-speed rotation to achieve a flat and smooth processing effect.
Common processing scenarios include: removing burrs or oxide layers, processing the contact surfaces of mechanical parts, and making plane references for molds or fixtures.
The task of the face milling cutter is to mount the face milling cutter firmly on the processing machine and transmit the rotation and cutting force.
In addition to one end of the face milling cutter handle that is connected to the machine, the other end has a structure designed specifically to lock the face milling cutter to ensure stability and no deviation during cutting.
Importance of face milling cutter handle:
- Key to stability:A good tool handle can effectively reduce vibration and improve the quality of the processed surface.
- Security assurance:Make sure the tool does not get loose to avoid machining accidents.
- Extend tool life:Reduce eccentricity and wear, allowing the blade to last longer.
Face milling cutter handles ensure quality
In the world of metal plane milling, the face milling cutter is the protagonist that directly contacts the workpiece and completes the cutting task, but what really gives this protagonist strength and stability is the seemingly ordinary but powerful face milling cutter handle. A high-quality tool handle can not only enable the face milling cutter to fully exert its cutting performance, but also fundamentally improve the overall processing efficiency, processing quality and safety. Below, we will reveal the core advantages of face milling cutter handles one by one.
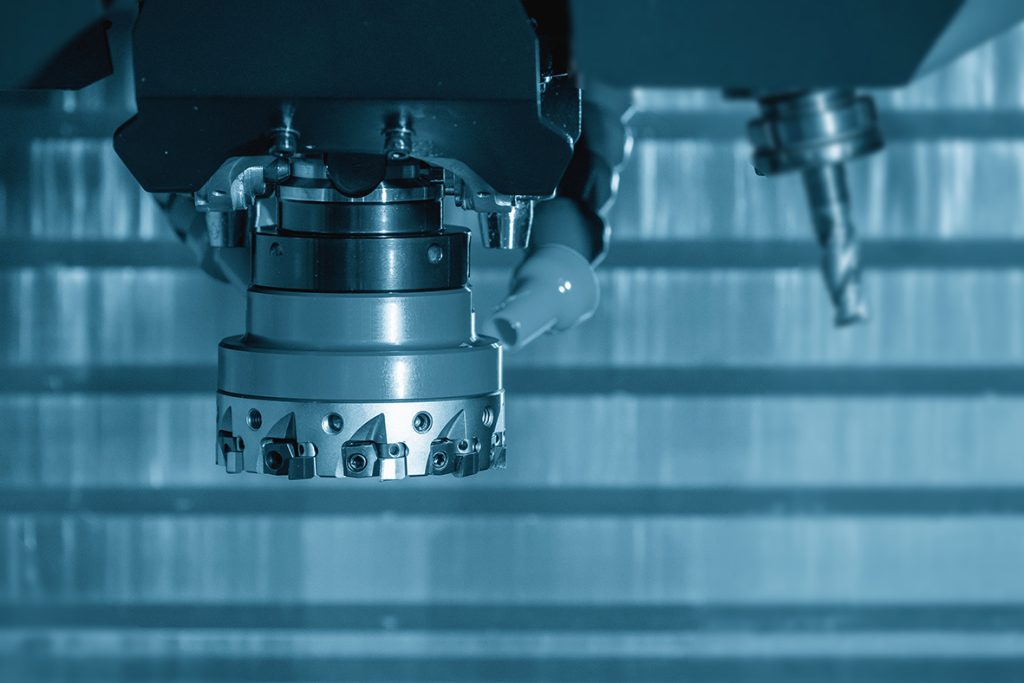
1. Rigid design: no more "shaking" during cutting
When the blade cuts into the metal surface, the cutting force is concentrated and released to the tool and the machine in a very short time. If the tool handle is not rigid enough, vibration will occur, which will not only cause ripples on the workpiece surface and reduce processing accuracy, but also significantly shorten the life of the blade. The high-rigidity face milling cutter handle adopts an integral forging or high-strength alloy structure, and the internal geometry is optimized through finite element analysis, so that it can remain as stable as a rock when subjected to large cutting forces.
2. Dynamic balance optimization: adapt to high-speed cutting requirements
As the spindle speed of CNC machines continues to increase, the dynamic balance level of the tool handle becomes a key indicator. Generally speaking, G2.5 can meet most medium and high speed machining needs. Through precision grinding and multiple dynamic balancing corrections, an excellent tool handle can reduce torque loss to an extremely low level and suppress vibration to a negligible range.
3. Internal Coolant Channel: Send Heat and Cutting Fluid to Where It’s Most Needed
When cutting under continuous heavy loads, high temperatures of the blade and chips are an unavoidable problem; rising temperatures can cause the blade to wear too quickly and even lead to thermal hardening and cracking of the surface. The face milling cutter handle with internal coolant channel design can guide the cutting fluid directly to the interface between the blade and the chip, quickly taking away the heat, discharging the chips, reducing the tool temperature and extending the service life.
4. Quick tool change and high compatibility
Modern automatic tool change production lines require fast and stable tool changes: any one second of idleness may cause the entire production line to stop. The face milling cutter uses common BT/HSK/PSA interface standards, combined with self-lubricating bumps or hydraulic locking mechanisms, so that the blade installation and removal can be completed within seconds, and ensure that each positioning is accurate to micron-level errors.
5. Safety and maintenance: reduce hidden worries and improve efficiency
From a factory management perspective, the risk of tool loosening is the most worrying. The high-quality handle features an innovative anti-drop structure on the cone surface and locking mechanism, which keeps the knife securely locked even in the face of strong vibrations. In addition, regular maintenance procedures—including taper cleaning, anti-rust lubrication, and regular dynamic balancing checks—can keep the toolholder’s performance stable and avoid unexpected downtime.
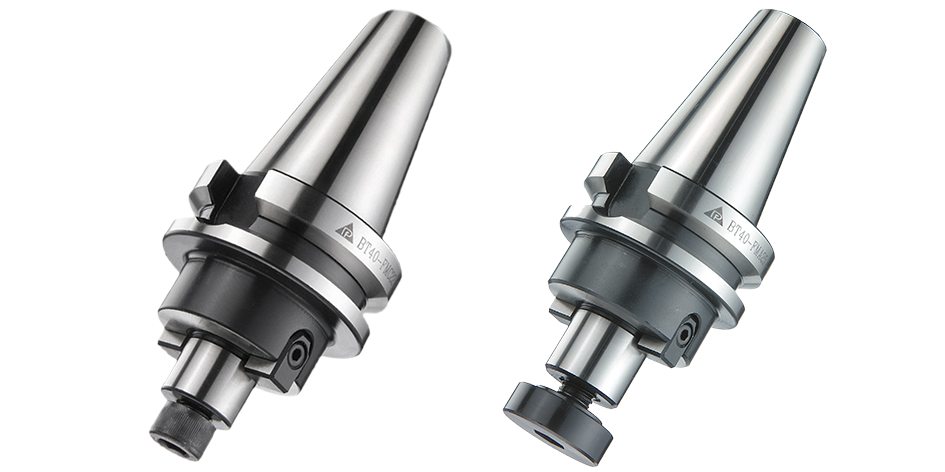
Choosing the right handle can make the face milling cutter shine
In today's manufacturing industry that pursues both high productivity and high quality, choosing a well-designed and rigorously manufactured face milling cutter handle is tantamount to building the most solid foundation for the entire production line. It may not "cut" directly like a blade, but it silently supports every precision cutting behind the scenes, allowing you to find the ideal balance between efficiency, quality and cost.
Know more1.pplication-Specific Holders Need a face milling tool holder? 2.pplication-Specific Holders Need a face milling tool holder?2