Understanding the HSK Tool Holder (Tool Holder) System - Tool Holder and Shank Parts
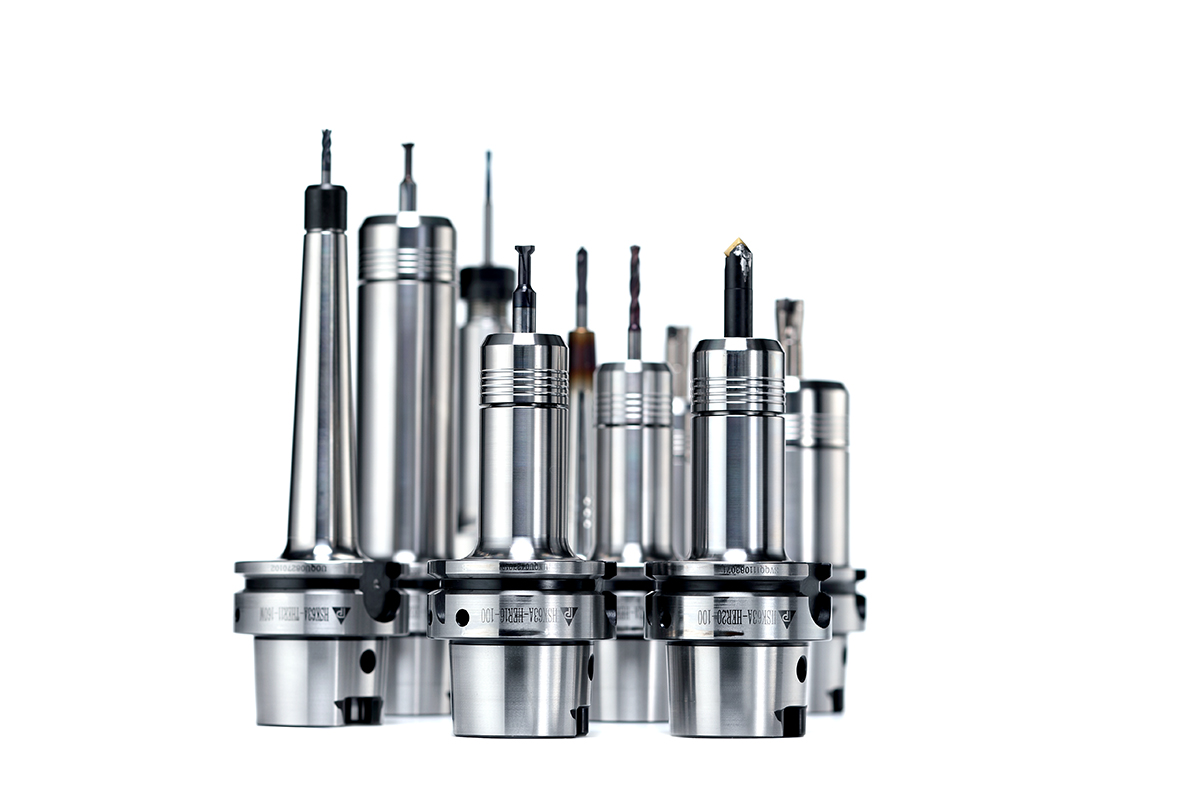
What is an HSK knife handle? What is its connection form?
HSK tool holder (tool holder) is a tool holder system invented in Germany with a hollow shank at the tail and a taper of 1:10. It is light in weight and short in stroke. The clamping tool holder has double-sided contact between the taper surface and the end surface. It is the most representative of double-sided clamping. The unique tool holder type has high static and dynamic stiffness and has become one of the important links in high-speed cutting.
The connection form of the HSK tool holder is that during the positioning and clamping process, the positioning surface of the tool holder and the equipment spindle must fit very tightly without any gaps that affect accuracy. The high system rigidity and dynamic balance also ensure that when the clamping mechanism is clamping the tool holder, the positioning surface will not change at all due to interference from external forces, and sufficient tightening must be maintained at all times during the clamping process. force.
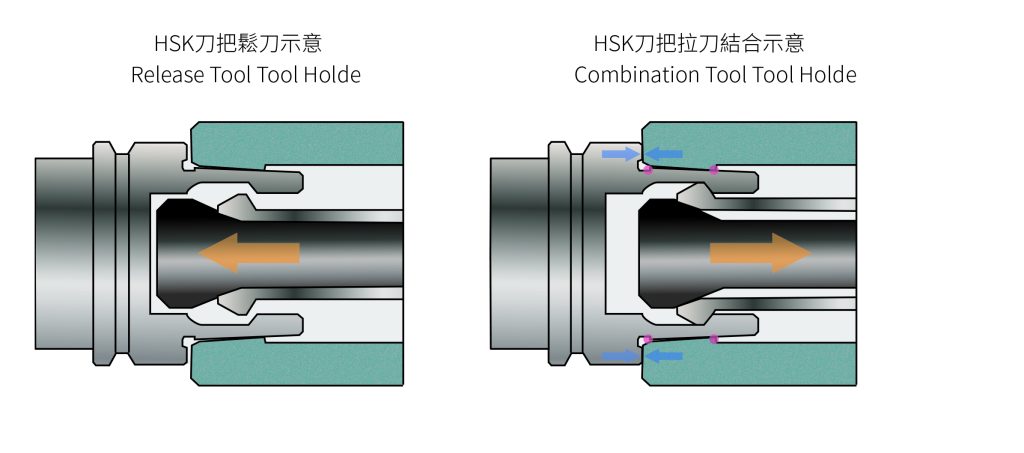
The form and characteristics of HSK knife handle
The main types and characteristics of HSK tool holders are formulated according to the specifications of DIN69893. The six main types of HSK tool holders are described.
Type A: general processing, high torque load, medium speed, automatic tool change
Type B: fixed application mode, medium torque load, high speed, automatic tool change
Type C: general processing, high torque load, medium speed, manual tool change
Type D: fixed application, medium torque load, high speed, manual tool change
Type E: high speed, high-speed cutting, low torque load, self-service tool change, easy balance
Type F: medium speed, processing soft materials, low torque, automatic tool change, Yipingjie
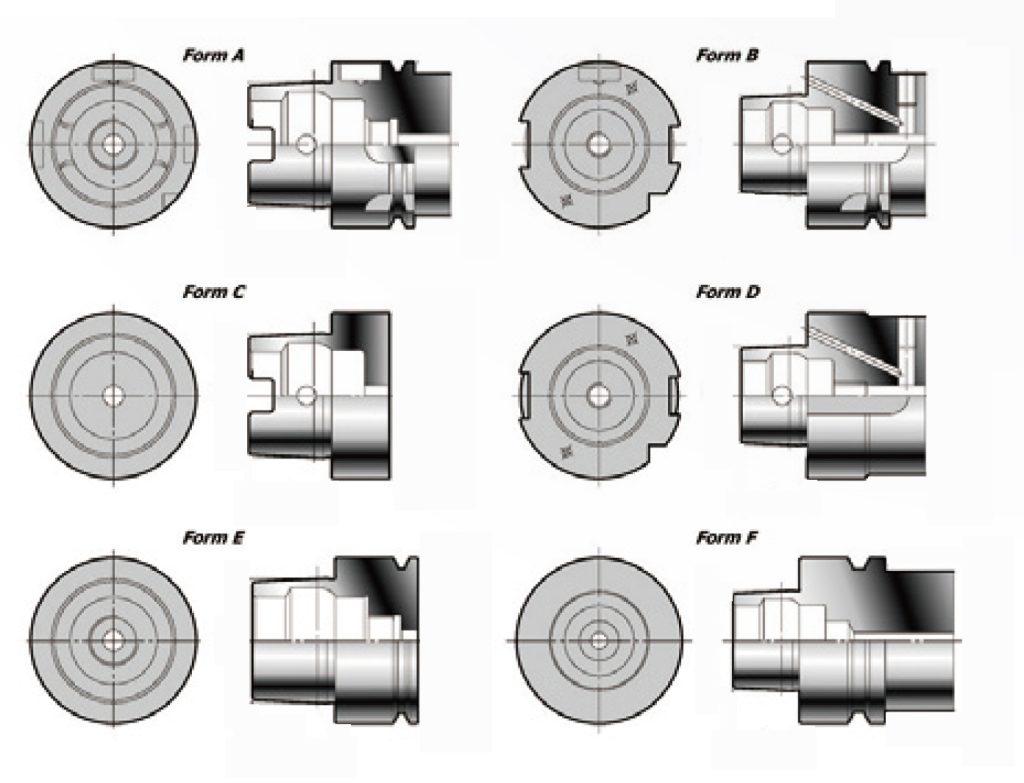
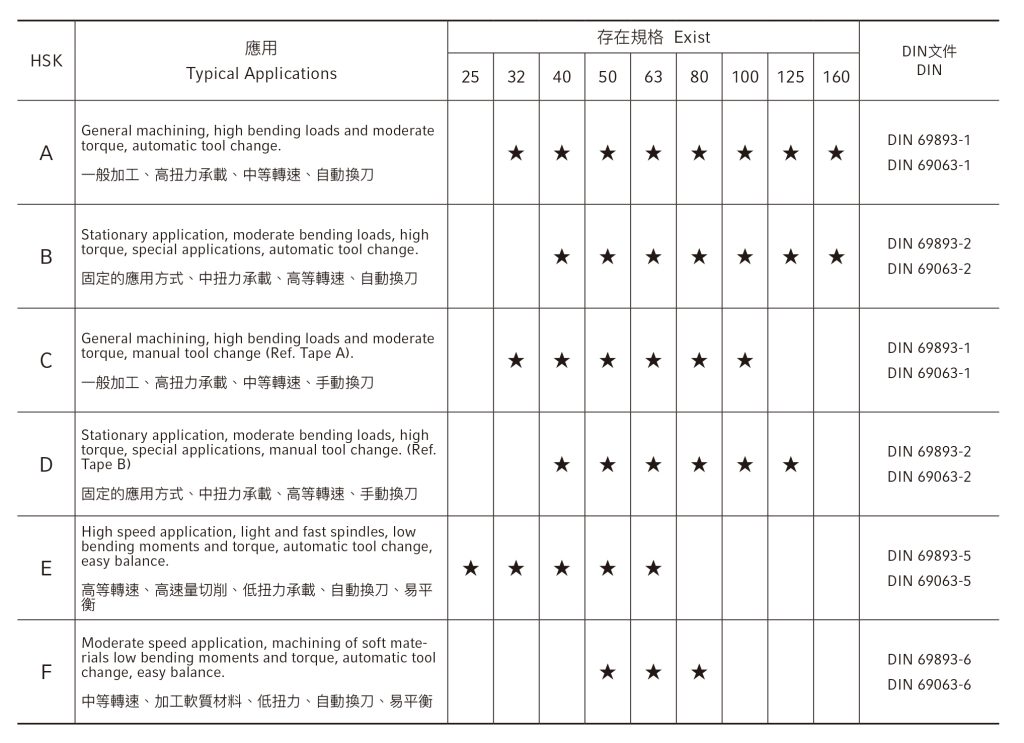
Dimensions and specifications of HSK-A and HSK-E tool holders
HSK-A with keyway and HSK-E without keyway are the more common automatic tool changing systems in machining centers:
HSK-A knife handle:Common specifications are HSK50A, HSK63A, and HSK100A. The larger the number, the larger the handle size, so HSK50A
HSK-E knife handle:Common specifications are HSK25E, HSK32E, HSK40E and HSK50E. The larger the number, the larger the handle size, so HSK25E
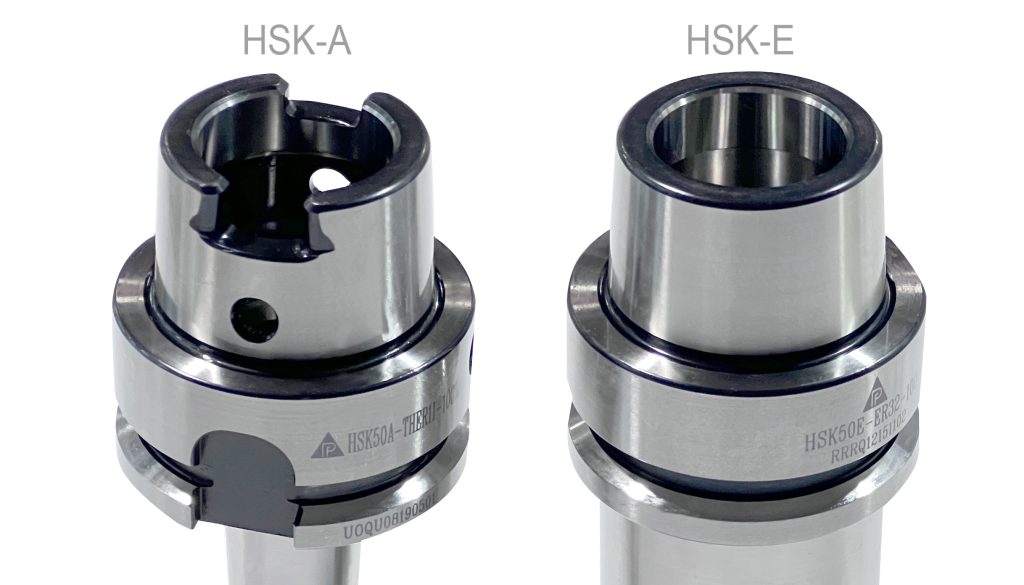
Technical characteristics of HSK tool holders
Double-sided contact design:The inner and outer conical surfaces of the HSK tool holder are in contact with the machine tool spindle at the same time, ensuring high positioning accuracy and rigidity and reducing runout during processing.
Good repeatability accuracy:The HSK tool holder can automatically compensate for thermal expansion during processing, maintaining processing accuracy and stability and ensuring processing consistency.
Lightweight design:Compared with the traditional BT tool handle, the hollow handle at the end of the HSK tool handle is designed with a taper of 1:10. Its light weight and short stroke reduce deformation caused by centrifugal force and the risk of the tool handle falling off.
More suitable for high-speed processing:The design of the spindle broaching mechanism makes the positioning and clamping of the tool handle very compact, without any gaps that affect accuracy. It is widely used in rotary tool clamping equipment of high-speed cutting machine tools. It plays the role of connecting the spindle of CNC machine tools and cutting tools and transmitting torque.
The difference between HSK tool holder (tool holder) and BT tool holder system?
HSK tool holder is a tool holder system with a hollow shank at the tail with a taper of 1:10. The connection form is that the inner and outer conical surfaces of the tool holder are in contact with the machine tool spindle at the same time. During the positioning and clamping process, the positioning surface of the tool holder is in contact with the equipment spindle. It is very compact and does not have any gaps that affect accuracy.
The BT tool holder adopts a large taper design of 7:24. The cone of the tool holder is in tight contact with the inner cone surface of the spindle under the action of the axial tension of the tie rod. The solid cone directly supports the tool in the taper hole of the spindle. , can reduce the overhang of the tool, which makes the contact area between the tool holder and the machine tool spindle larger, providing higher rigidity and stability.
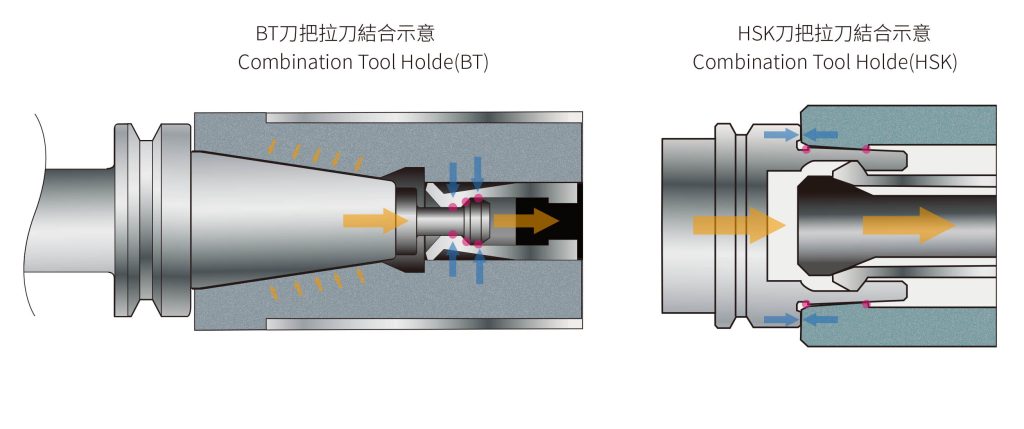
To learn more, please go to the official website:Precision tool handle selection HSK-A/HSK-E series selection