Collets – The Essential Companion to CNC Tool Holders
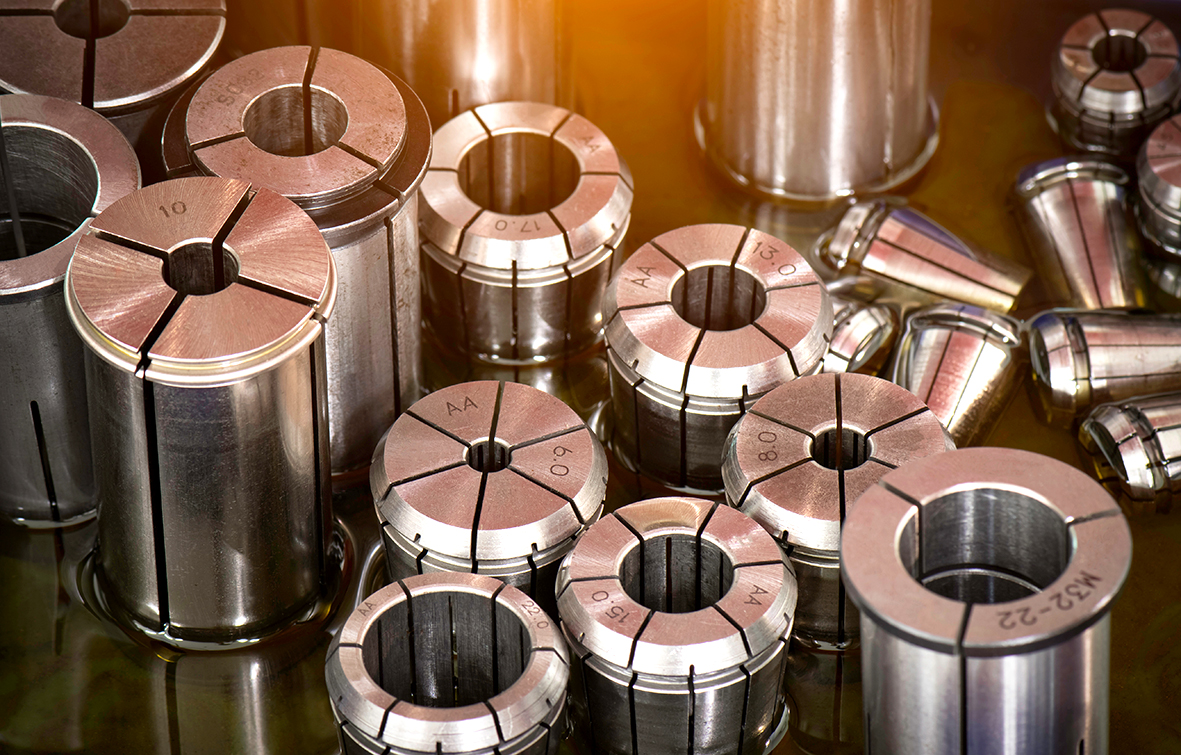
In the ever-evolving world of CNC machining, precision, efficiency, and stability are the three pillars every metalworking professional strives to achieve. While the tool holder is often the focal point of most tooling systems, there's one crucial component that frequently goes unnoticed — the collet. Acting as the vital link between the cutting tool and the holder, a collet’s gripping performance directly impacts machining accuracy, tool life, and overall machine stability. In this article, we’ll explore the functions, types, and maintenance tips for collets, helping you build a more competitive CNC machining solution.
What Is a Collet? The Unsung Hero of Precision Machining
A collet is a cylindrical, elastic clamping device with a tapered outer surface and a straight inner bore. It is typically paired with a clamping nut or cap and installed into the tool holder. When the nut is tightened, the collet contracts uniformly, securely gripping the shank of the cutting tool. This design ensures reliable holding even under high-speed rotation, achieving excellent repeatability and minimal runout. Especially in high-speed, high-precision CNC milling and drilling operations, collets play a behind-the-scenes yet indispensable role.
Understanding the ER Series: The Most Widely Used Collet System in CNC Machining
In-Depth Analysis of ER Collets: The Universal Precision Clamping Tool for CNC Machining
1. Origins and Standardization of the ER Collet
Developed in 1972 by Rego-Fix of Switzerland, the ER collet system quickly became an international standard — conforming to both DIN 6499 (European Standard) and ISO 15488 (Global Standard). Its flexibility and broad clamping range have made it a go-to solution for various machining applications, including milling, drilling, tapping, and engraving. Today, ER collets are the most widely used and mature collet system in the CNC industry.
2. Structure and Operating Principle
ER collets typically feature 8 to 16 longitudinal slits (often referred to as "elastic slots") that allow for uniform radial contraction when axial force is applied. During installation, the collet is placed into the nut’s groove and then screwed into the tool holder. As the nut tightens, it pushes the collet into the taper bore of the holder, generating radial gripping force that securely clamps the tool shank.
- Uniform 360° grip (avoiding point-loading)
- Elastic fit that compensates for ±0.5mm shank size variation
- Quick tool changes for improved production efficiency
3. Common Sizes and Clamping Ranges (ER11–ER40)
Collet Type | Max Diameter (mm) | Recommended Clamping Range (mm) | Outer Diameter (mm) | Length (mm) |
ER11 | 7.0 | 1~7 | 11.5 | 18 |
ER16 | 10.5 | 1~10 | 17 | 27.5 |
ER20 | 13.0 | 1~13 | 21 | 31.5 |
ER25 | 16.0 | 1~16 | 26 | 34 |
ER32 | 20.0 | 2~20 | 33 | 40 |
ER40 | 26.0 | 3~26 | 41 | 46 |
Each ER size is typically used with a matching collet set, allowing flexible selection based on tool shank diameter. Always stay within the specified range for optimal performance.
4. Key Advantages of ER Collets
High Precision: Runout accuracy up to 0.002–0.006mm depending on grade, ideal for demanding milling, boring, and drilling.
Wide Clamping Range: ±0.5mm flexibility per collet size.
Modular System: Compatible with a variety of nuts, holders, and ER extension holders for streamlined tool management.
Excellent Stability: Supports high-speed spindles (25,000+ rpm) while reducing vibration and machining errors.
Easy Maintenance: Modular structure offers cost-effective maintenance and convenient replacement.
5. Ideal Applications
- Milling: Suitable for both roughing and finishing, especially high-speed milling.
- Drilling: Ensures secure holding of straight shank drills for improved hole accuracy.
- Tapping: When used with anti-rotation devices, offers precise tapping depth control.
- ATC Systems: Well-suited for automated tool change environments.
- ATC Systems: Well-suited for automated tool change environments.
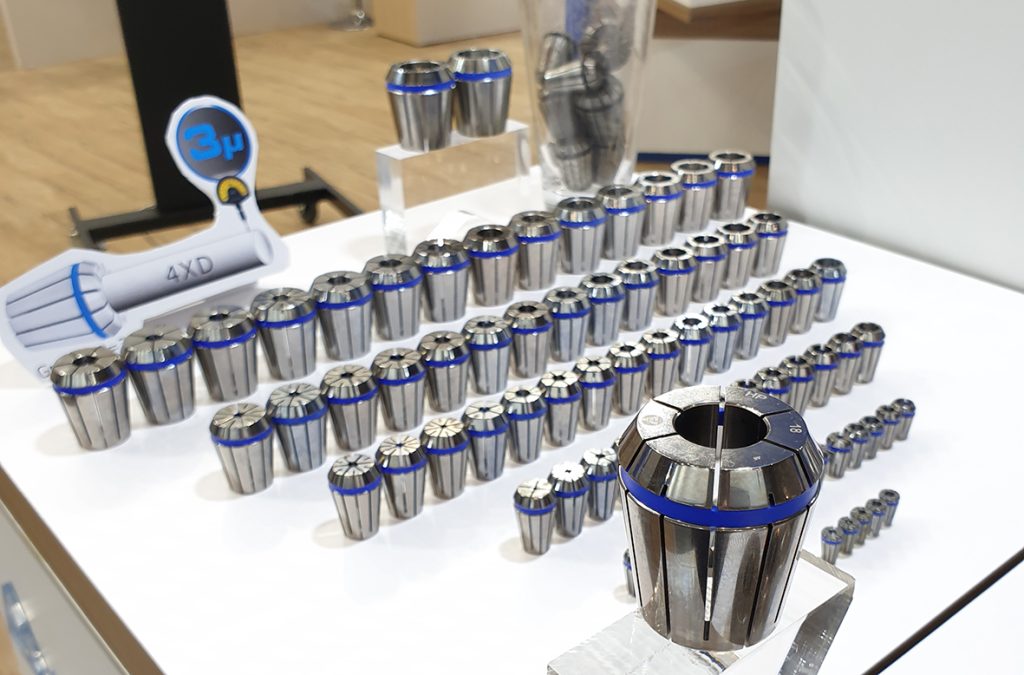
TG Collets: Designed for higher torque applications. Offer stronger gripping force but are bulkier and less flexible, often used in heavy drilling or roughing operations.
DA (Double Angle) Collets: An older design, more affordable but generally less stable and precise than ER collets. Gradually being phased out.
OZ Collets: Hexagonal exterior with excellent grip strength, commonly found in woodworking or auto tool-change engraving machines.
Autolock Collets: Designed for threaded-shank tools; automatically locks during insertion. Ideal for high repeatability production lines.
Collets and Tool Holders – A System That Defines Performance
Tool holders such as BT30, BT40, HSK63, ISO40, and CAT40 require matching collets and nuts. ER collets, for instance, are compatible with a wide range of holders. By simply changing the internal collet and nut, users can accommodate various tool shank sizes, improving flexibility and cost efficiency. However, using the wrong collet or applying insufficient torque can lead to excessive runout, tool slippage, or even dangerous machining failures.
Why Choose High-Quality Collets?
Premium collets significantly reduce tool runout and vibration, resulting in better surface finish and extended tool life. Stable clamping also contributes to machine dynamic balance and overall productivity. In contrast, cheap or overused collets may suffer from metal fatigue, deformation, and loss of grip — all of which compromise machining quality and risk damaging expensive equipment. That’s why choosing collets manufactured with strict tolerances, precision grinding, and proper heat treatment is critical for CNC stability and safety.
Maintenance and Replacement – The First Step to Precision Machining
To maintain optimal clamping and safety, clean the collet and nut contact surfaces each time you change tools. Use an air gun to blow off chips and wipe down any oil or debris with a dry cloth and degreaser. Over time, metal fatigue may reduce a collet’s elasticity and grip, causing uneven clamping. Depending on usage frequency, it is recommended to replace collets every 2–3 months for standard operations, or more frequently in high-volume production lines. Periodically check for wear at the nut and holder interface to ensure continued balance and safety.
Choose the Right Collet – Elevate Your Machining Quality
Though small in size, collets are a critical component of any CNC tooling system. Selecting high-quality collets tailored to your application needs — combined with proper maintenance and replacement practices — will allow you to fully harness the precision and efficiency of your tool holders. At PARFAITE, we specialize in high-precision, high-rigidity collet and tool holding solutions. Whether you're working in metal milling, drilling, mold making, or automated production, the right collet–holder combination will help you achieve the next level of machining performance.
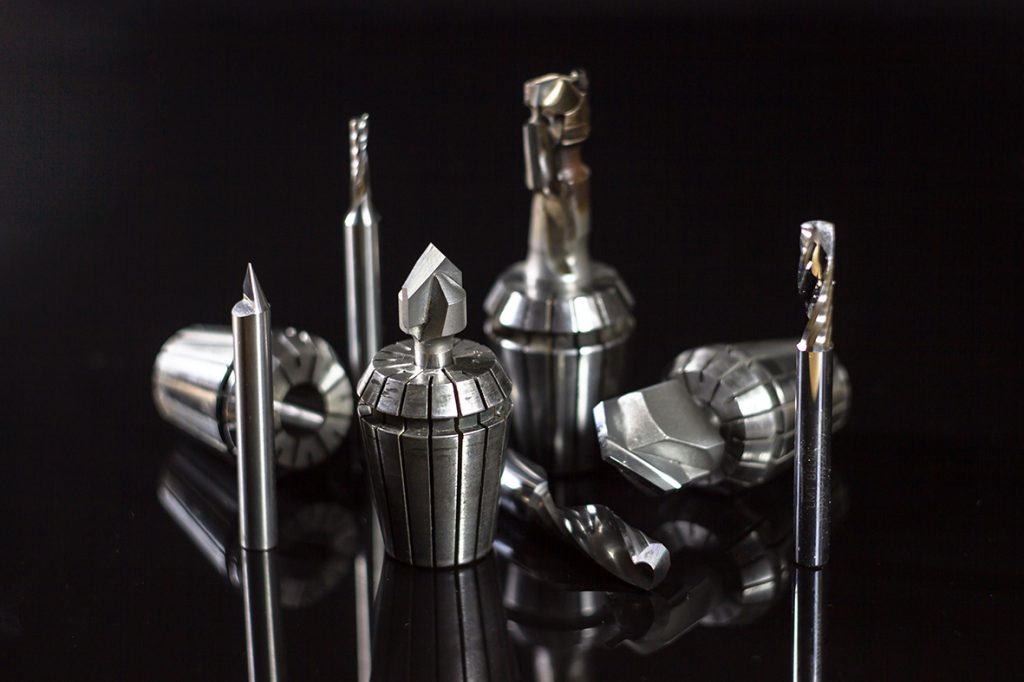