Complete Guide to Cutting Tools: Types, Materials, and Selection Tips
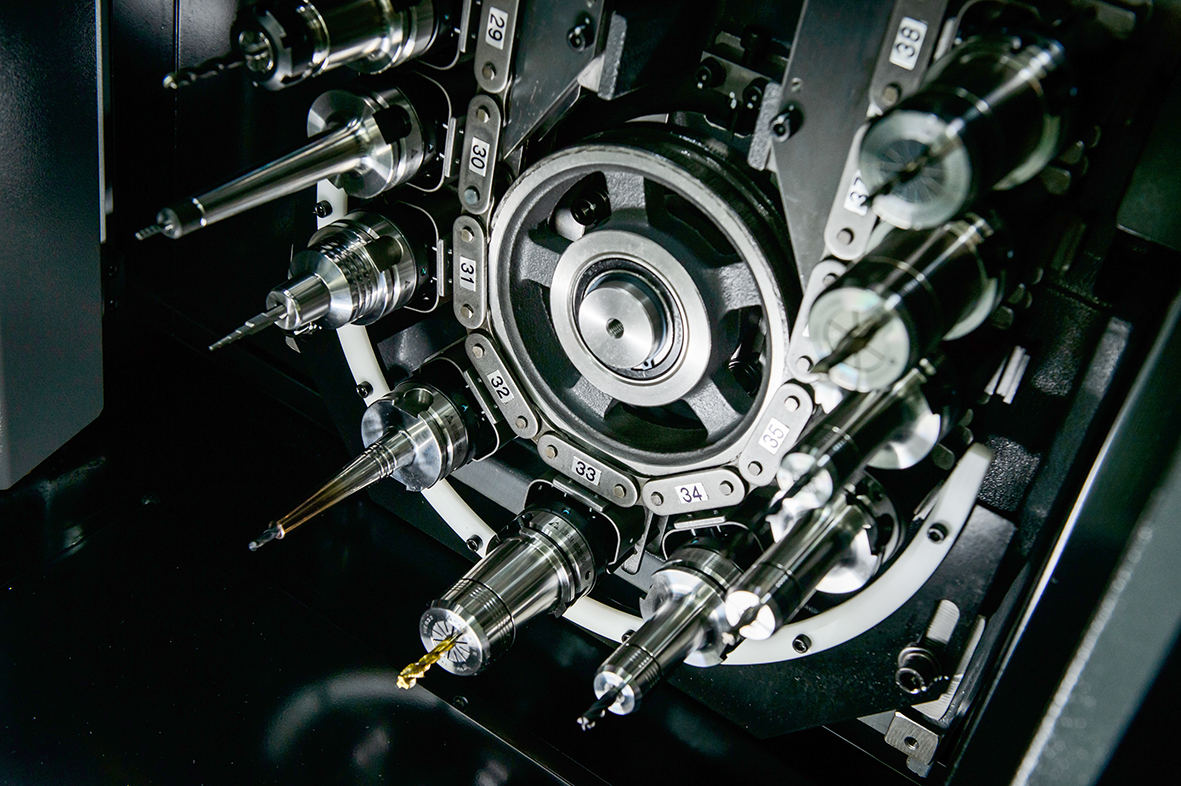
What Are Cutting Tools and Why Do They Matter?
Cutting tools are essential instruments used to remove material from a workpiece, transforming raw materials into precise shapes through processes such as rotation, feed, and pressure. Whether it's metal machining, plastic forming, or composite material cutting, tool performance and precision directly impact product quality. High-quality cutting tools reduce vibration and runout, improve machining speed and surface finish, and extend equipment life while minimizing tool change frequency. They are crucial to boosting machining efficiency and controlling costs.
In real-world applications, tools must not only perform accurate cuts but also endure extreme conditions such as high-speed rotation, intense cutting forces, and high-temperature friction. That’s why different materials, coatings, and geometrical designs are developed to optimize performance for specific workpiece materials and machining methods. Furthermore, modern manufacturing places greater emphasis on tool life stability, replacement efficiency, and cost-effectiveness—making cutting tools not just consumables, but strategic assets that enhance production competitiveness.
Common Types of Cutting Tools: Choosing the Right Tool for the Job
Cutting tools come in various types and designs tailored to different machining needs and applications. Common categories include:
Drill Bits: Designed for hole-making operations. From standard through-holes to complex angled or deep-hole drilling, there are suitable types such as center drills, twist drills, and deep-hole drills.
End Mills: Versatile tools used for face milling, side milling, contouring, and slotting. They are a staple in CNC milling and come in various forms like 2-flute, 4-flute, and ball-nose end mills—each suited for different depth and finish requirements.
Reamers: Ideal for refining hole diameters and improving hole accuracy and surface finish.
Thread Mills: Replacing traditional taps, thread mills can cut high-precision internal and external threads, especially suitable for hard or thin-walled materials.
Turning Tools: Used on lathes for external, internal, or face turning. Available in roughing or finishing variations depending on the machining task.
Understanding the purpose and differences of each tool type improves selection efficiency and lays a solid foundation for setting cutting parameters and managing tool life.
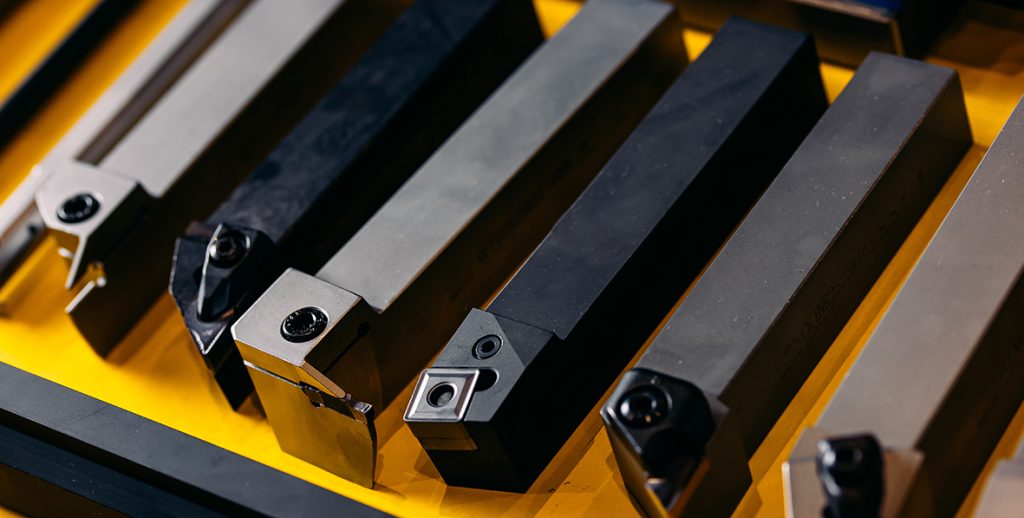
Anatomy of a Cutting Tool: Every Detail Matters
A high-performance cutting tool is more than just a sharp edge—it relies on the harmony of its overall structure. A typical cutting tool comprises three main components:
Insert / Cutting Edge: The core of the cutting process. Geometry and material affect cutting resistance, chip evacuation, and surface finish. Many tools use replaceable inserts for easier maintenance.
Tool Holder: The critical interface between the tool and machine. Its rigidity and dynamic balance directly influence cutting stability. PARFAITE’s high-precision tool holders offer outstanding concentricity and balance, making them ideal for high-speed and heavy-duty machining. Compatible with standards such as HSK, BT, and CAT, they ensure secure clamping and efficient tool changes.
Coolant Channel Design: For high-temperature or difficult-to-machine materials, some tools and holders feature internal coolant channels to aid in heat dissipation, chip removal, and tool life extension. PARFAITE’s coolant-through holders support this feature, widely adopted in aerospace and stainless steel machining.These structural elements work in unison to create a truly efficient and stable cutting system.
Materials and Coatings: The Core of Performance and Tool Life
The effectiveness of a cutting tool lies in the synergy between its base material and surface coating. Common tool materials include:
High-Speed Steel (HSS): Offers good toughness and machinability, ideal for low-speed or manual operations.
Carbide: Known for its high hardness and heat resistance, carbide tools dominate CNC automated machining.
CBN, PCD, and Ceramic Tools: Used in high-hardness or non-metallic material applications, these represent the high-performance tier of cutting tools.
Coatings play a pivotal role in tool longevity and machining quality:
TiN, TiAlN, AlCrN: Enhance hardness and oxidation resistance.
DLC (Diamond-Like Carbon): Ideal for aluminum or sticky materials, effectively reducing built-up edge (BUE).
DLC (Diamond-Like Carbon): Ideal for aluminum or sticky materials, effectively reducing built-up edge (BUE).
Selecting the appropriate coating based on workpiece material, cutting temperature, and process type is essential to maximizing tool performance.
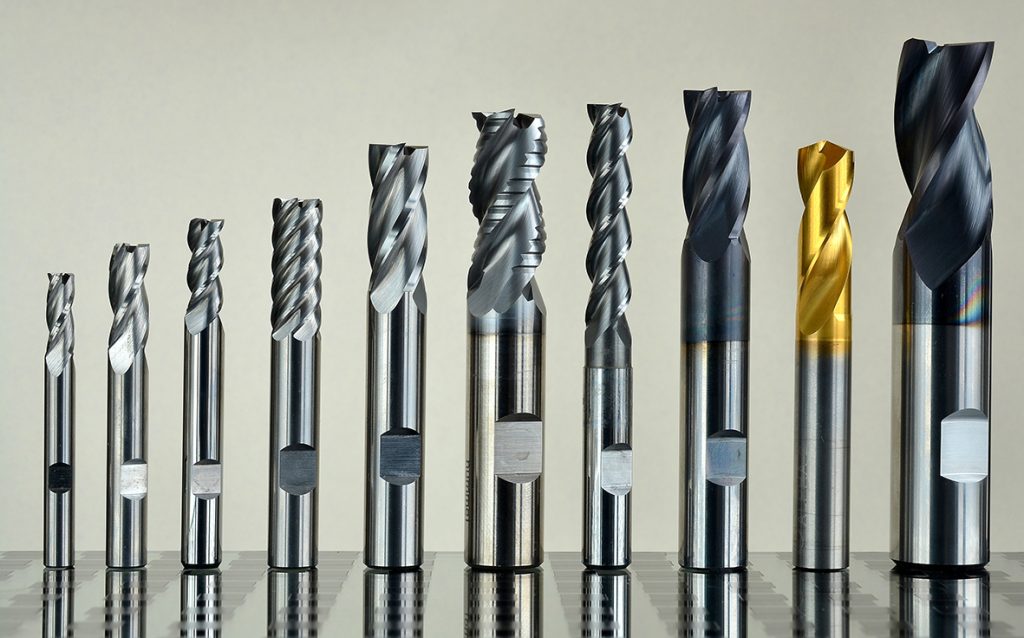
Choosing the Right Tool: Balancing Performance and Cost
With so many options available, manufacturers often ask: “Which cutting tool should I use?” The key isn’t about choosing the strongest tool, but rather the most suitable one for the specific application. The ideal tool selection depends on several factors:
Workpiece Material: Aluminum benefits from sharp edges with minimal or low-friction coatings. Steel requires wear-resistant coatings and harder substrates.
Machining Method: Roughing demands high-rigidity tools, while finishing focuses on precision and surface quality. Threading or drilling requires dedicated tool designs.
Machine and Tool Holding System: High-speed machines require well-balanced tools and holders. Compact machines prioritize lightweight and stability. PARFAITE offers a wide range of holders to match different machine characteristics and optimize system performance.
Production Rate and Cost Considerations: For mass production, indexable tools reduce downtime. For high-value parts, precision tools with extended life reduce the risk of error.
Choosing the right tool is like selecting the right general—success depends on strategic fit.
Monitoring Tool Wear: Timely Maintenance to Avoid Risk
All cutting tools wear over time. If wear goes unnoticed, it can affect dimensional accuracy and surface finish. Common types of tool wear include:
Flank Wear: Leads to size deviations.
Edge Chipping: Causes instability and tool breakage.
Edge Rounding: Results in poor surface roughness.
In addition to visual inspection, manufacturers can implement RFID-based tool management systems to track usage, machining hours, and wear history. PARFAITE’s RFID tool management solution gives each tool a digital identity, enabling integration with machines for automated tool change, lifetime alerts, and maintenance reminders.
With data-driven tool management, you can maximize tool usage, reduce unplanned downtime, and build a smarter, more efficient production workflow.
Precision Tools for a Smarter Manufacturing Future
Though small in size, cutting tools are at the heart of precision machining. From understanding tool types and construction to mastering material selection, application, and lifecycle management—every detail holds the key to higher productivity and better quality.
PARFAITE specializes in integrated tool system solutions and intelligent manufacturing support. Whether you're in metalworking, mold making, or high-precision component manufacturing, we offer expert tool holder solutions and management technologies to help you improve machining performance, reduce production risk, and cut precisely toward the future.
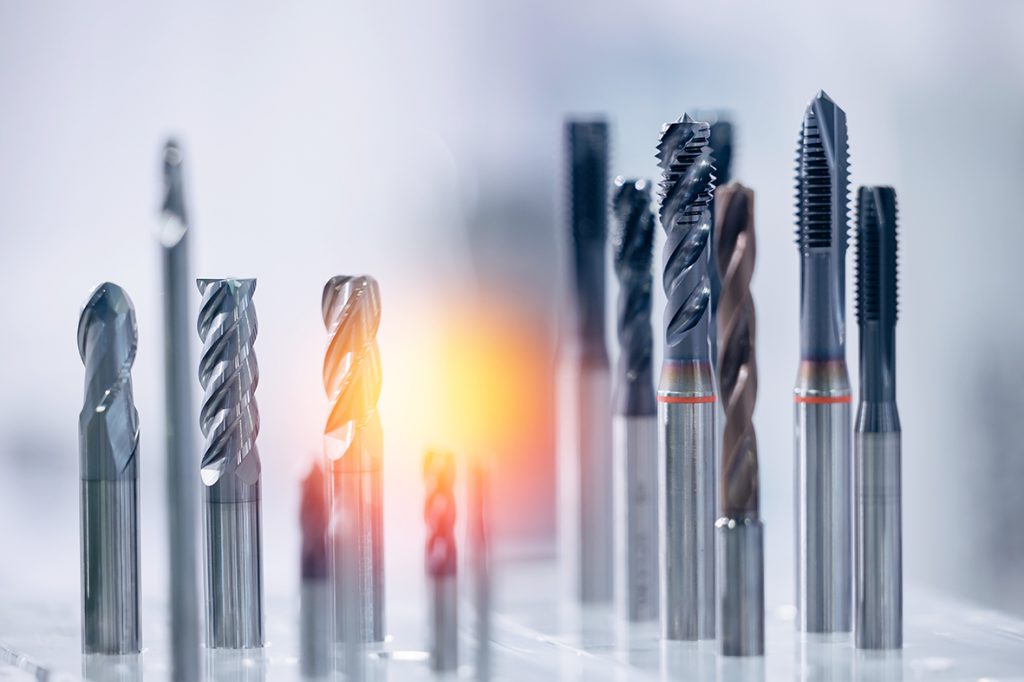