An Overview of the Applications of Drill Chucks and Specialized Tool Holders
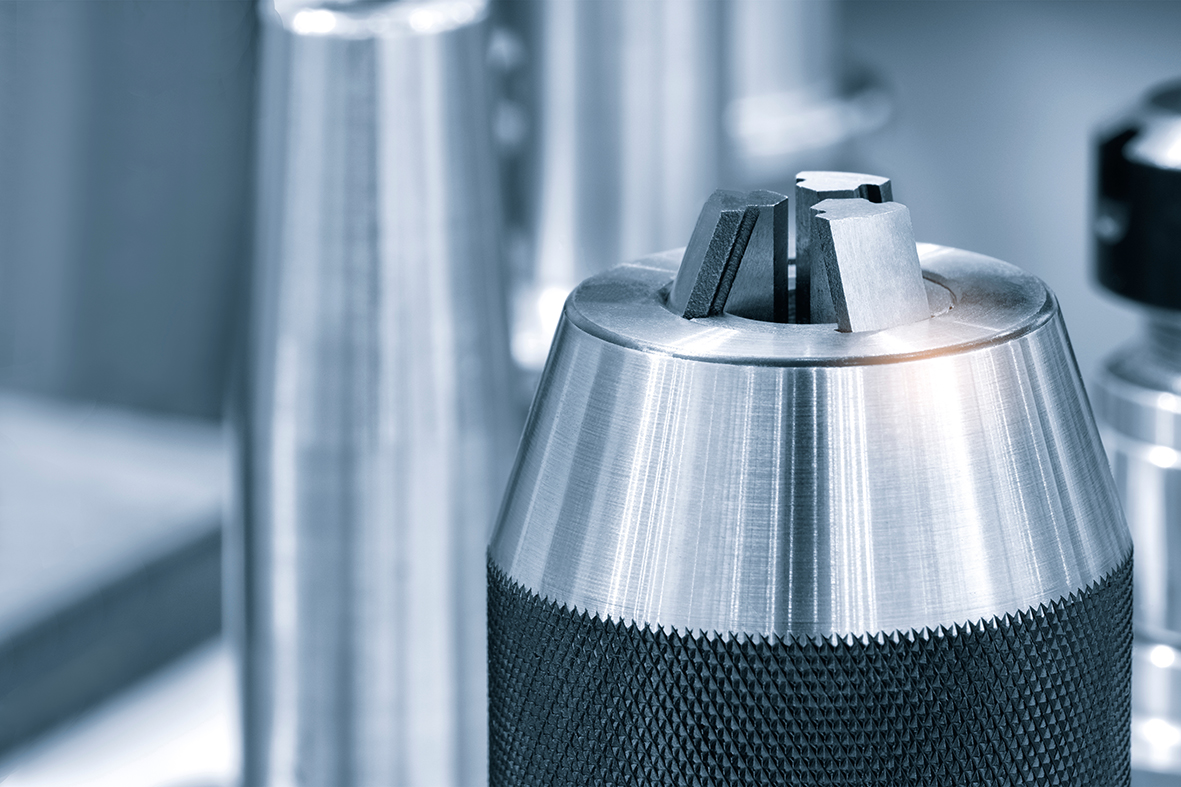
In the field of modern metal processing, drilling is an indispensable basic process. In order to ensure the accuracy and stability of drilling, choosing the right drill chuck and matching tool handle is one of the key factors for stable processing quality. This article will give you an in-depth understanding of the drill chuck and its corresponding tool holder system, and explain how the two work together to meet diverse processing needs.
Introduction to the functions and types of drill chucks
A drill chuck is a device for holding drill bits and is widely used in drilling machines, milling machines and CNC machining centers. It aligns and fixes the drill bit through an internal three-claw structure to achieve stable drilling operations. The three-jaw clamping mechanism has an automatic centering function, which can effectively reduce eccentricity and runout during processing and improve hole position accuracy.
Common drill chuck types include:
1. Key type drill chuck
Locking is done with a special key, providing strong clamping force. Especially suitable for situations where heavy cutting or long processing time is required. It has high stability and firm clamping, and is a commonly used chuck type for precision machining.
2. Self-tightening drill chuck
It can be directly tightened by hand, which is quick and convenient to operate. It is suitable for frequent tool changes or small and medium-sized drilling operations. Although the clamping force is slightly lower than the key type, it is very practical for high-variety and small-batch production.
The clamping range of drill chucks usually ranges from 0.5 mm to 16 mm, and different specifications and accuracy levels can be selected according to application requirements (for example, those with runout controlled within 0.05 mm are high-precision drill chucks).
Special handle for holding drill chuck
The tool holder is the key connecting component between the drill chuck and the machine tool spindle, and its design directly affects the clamping rigidity and machining accuracy. According to different machine specifications, common tool handle standards are as follows:
- BT Type (BT30 / BT40 / BT50)
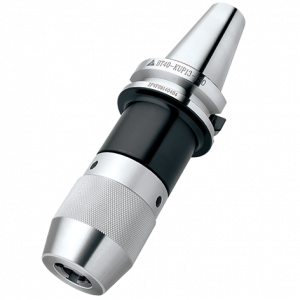
The front end of the tool handle is provided with a tapered hole for matching with the drill chuck. Common interface specifications include JT (Jacobs Taper), B (Morse/Brown & Sharpe Taper), etc., such as JT6, JT33, B16, etc. When using, you must ensure that the tapered shank at the rear end of the drill chuck matches the tapered hole size of the tool handle to ensure a secure installation and stable processing.
In addition, for applications requiring high speed, it is recommended to use high-speed tool holders with dynamic balancing, such as the HSK series, which can effectively reduce vibration and vibration during processing and improve processing quality and tool life.
Key points and application suggestions for matching drill chuck and tool handle
Although the drill chuck and the tool handle are two independent components, they need to work closely together in application. Here are some important suggestions for purchasing and using:
1.Specification matching is the most important: Make sure the taper of the drill chuck and the taper of the tool holder are of corresponding sizes, such as B16 with B16, JT6 with JT6.
2.Processing demand-oriented selection:
- High rigidity drilling → Key-type chuck + BT/HSK tool holder is preferred
- Rapid tool change requirements → Can be matched with self-tightening chuck + standard tool handle
3.Controlling the jump value:To ensure the accuracy of hole position and hole diameter, high-precision chuck and tool handle with run-out error less than 0.05 mm should be selected, and attention should be paid to correct installation.
4.Clamping depth recommendations: The drill bit should be inserted into the drill chuck at least 2/3 of the jaw length to avoid loosening or slipping.
A good match between the drill chuck and tool handle can not only improve the accuracy of drilling, but also reduce tool wear, extend the service life of the machine, and significantly improve the overall processing efficiency.
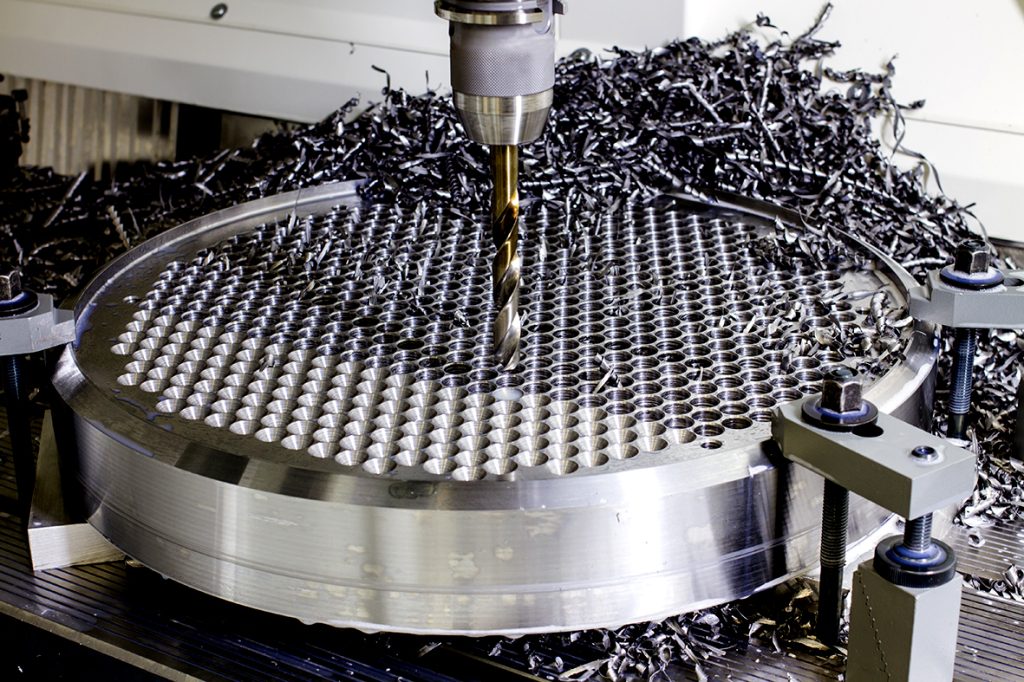
For drill chuck handle specifications, please visit the official website.Learn more about the specifications