Introduction to Hydraulic Tool Holder (Hydraulic Tool Holder) - Clamping

Basic principles of hydraulic tool handles
Hydraulic tool holder, also called hydraulic tool holder, is a high-precision clamp that uses hydraulic technology to hold tools. Its working principle is to use the pressure of the internal hydraulic chamber to clamp the tool. When the bolt or oil filling hole in the tool holder is adjusted, the hydraulic oil will flow and generate uniform pressure, so that the tool is stably fixed in the tool holder. Compared with the traditional collet-type clamping method, the hydraulic toolholder provides higher clamping accuracy, faster clamping tool change method and reliable and stable repeatability, and is suitable for extremely demanding finishing processes.
The hydraulic tool handle is made of high-quality alloy material. The internal structure usually consists of a hydraulic chamber, an oil seal and a pressure regulating device. These designs ensure that the tool can withstand high-speed and high-torque processing requirements while reducing processing errors caused by unstable clamping.
Advantages of hydraulic tool handles
The biggest advantage of the hydraulic tool holder is its excellent 3μ clamping accuracy and stability. The accuracy of the Puhui hydraulic tool holder is measured at 4 times the tool shank diameter (maximum 80mm). Since the hydraulic system can provide uniform and stable clamping force, the tool is less likely to deflect during processing, which can significantly improve processing quality. In addition, it is easy to operate. You only need to adjust the bolts or add oil to complete the installation and disassembly of the tool, saving a lot of man-hours.
Another important advantage is reduced tool wear. Because the hydraulic clamping method can evenly distribute the clamping force, it avoids the stress concentration caused by point contact in traditional clamps, thereby extending the tool life. In addition, the hydraulic toolholder can effectively reduce vibration and improve processing stability when running at high speeds, and is especially suitable for high-precision machining and high-speed cutting application scenarios.
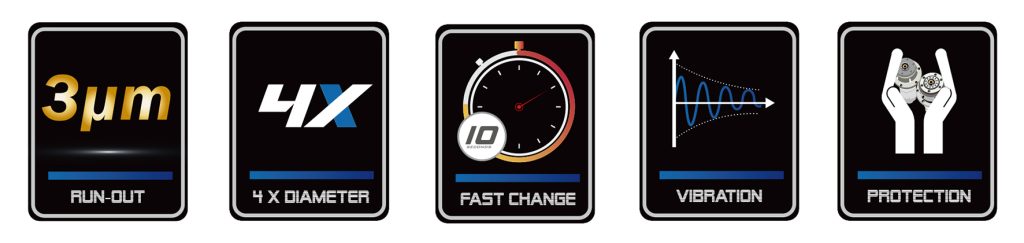
Application range of hydraulic tool handle
Hydraulic tool holders are widely used in various metal processing fields, including milling, reaming and other operations. Especially in situations where high precision and stability are required, such as aerospace, automotive industry and medical device manufacturing, hydraulic toolholders can ensure the dimensional accuracy and surface quality of the workpiece being processed.
In complex-shaped mold processing, hydraulic toolholders are favored for their high stability. It can effectively reduce the risk of tool breakage and shorten processing time. At the same time, when processing high-hardness materials such as titanium alloy and stainless steel, the stability and accuracy of the hydraulic tool holder are particularly important, and can effectively meet the processing challenges of such materials.
Selection and maintenance of hydraulic tool handles
Choosing the right hydraulic toolholder requires consideration of many factors, including machining needs, tool specifications and machine tool performance. Different brands of hydraulic tool holders may have differences in hydraulic pressure range, clamping diameter and durability, so you should compare them carefully when purchasing. Users should choose specifications that match the machine tool spindle, and select the appropriate clamping method and accuracy level based on the processing materials and process requirements. When clamping, the tool needs to be in 360-degree full circle contact, and the shank diameter of the matching tool needs to be h6 tolerance.
In terms of maintenance, the hydraulic tool handle needs to regularly check the status of the hydraulic oil and the integrity of the oil seal to ensure its normal operation. In the normal state without clamping the tool, the hydraulic locking screw should be loosened to the relaxed state. If it is locked without the tool being installed, the inner diameter of the hydraulic tool handle will be deformed and the accuracy of the hydraulic tool handle will be deteriorated.
After the workpiece is processed and will not be processed for a long time, it is best to withdraw the tool and keep the tool handle in a relaxed state, so as to maintain good accuracy and life of the tool handle.
In addition, the knife handle should be protected from strong impact and treated with anti-rust treatment when not in use to extend its service life.
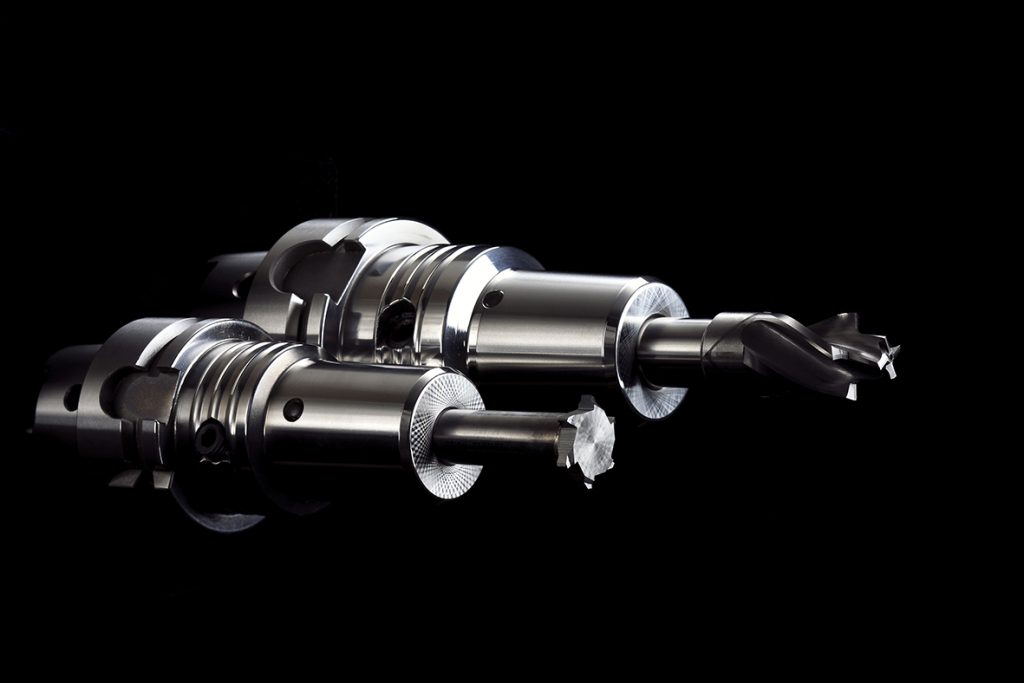
The future development of hydraulic tool handles
With the rapid development of intelligent manufacturing and automation technology, the future of hydraulic toolholders will develop towards higher precision and intelligence. For example, an intelligent hydraulic toolholder combined with sensing technology can monitor the clamping force and processing status in real time, and transmit the data to the machine tool control system for analysis and adjustment. In addition, the application of new materials and manufacturing technologies will further enhance the durability and performance of hydraulic tool handles.
Environmental protection and energy saving will also become important directions in the design of hydraulic tool handles in the future. By improving the hydraulic oil formula and optimizing the design structure, future hydraulic toolholders will be able to reduce energy consumption while maintaining high performance. These innovations will bring higher efficiency and competitiveness to processing machine manufacturers.
In summary, hydraulic toolholders play an indispensable role in modern machining technology. Its characteristics of high precision and high stability not only meet the current needs of the manufacturing industry for high-efficiency processing, but also provide broad space for the advancement of future processing technology. Through continuous technological innovation and design improvement, hydraulic toolholders will be able to adapt to diverse processing scenarios more efficiently, helping operators improve production efficiency and quality, and cope with fiercely competitive market challenges. In the future, with the integration of intelligent and environmentally friendly technologies, hydraulic toolholders are bound to exert greater potential and value in the field of precision machining, bringing more opportunities and breakthroughs to the manufacturing industry.
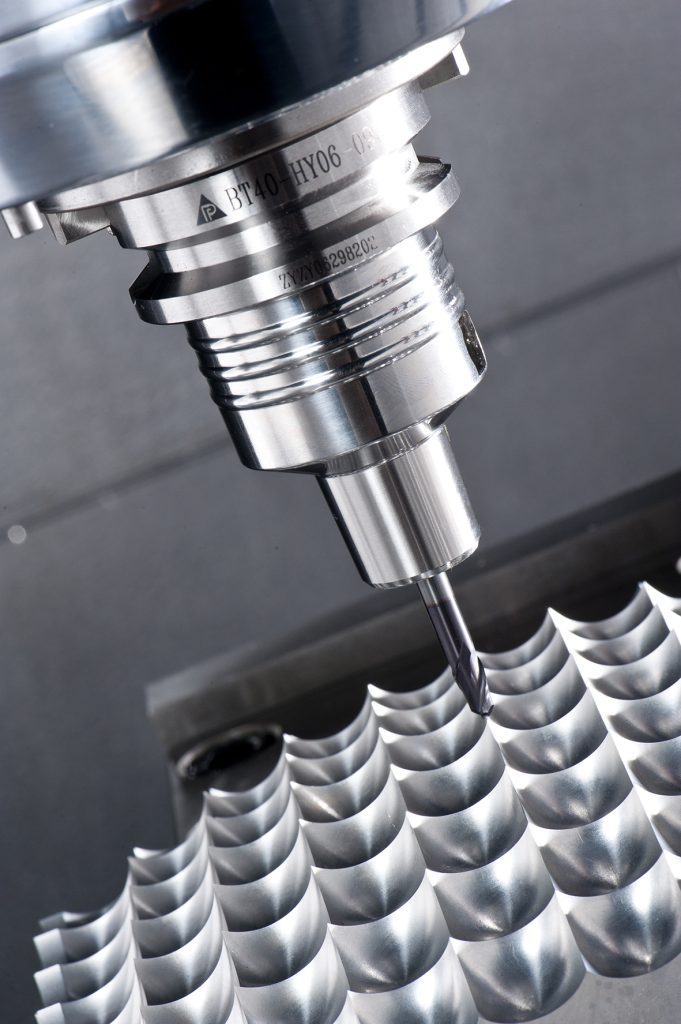