Comprehensive Guide to Milling Cutter Types and Tool Holder Clamping System Selection for CNC Machining
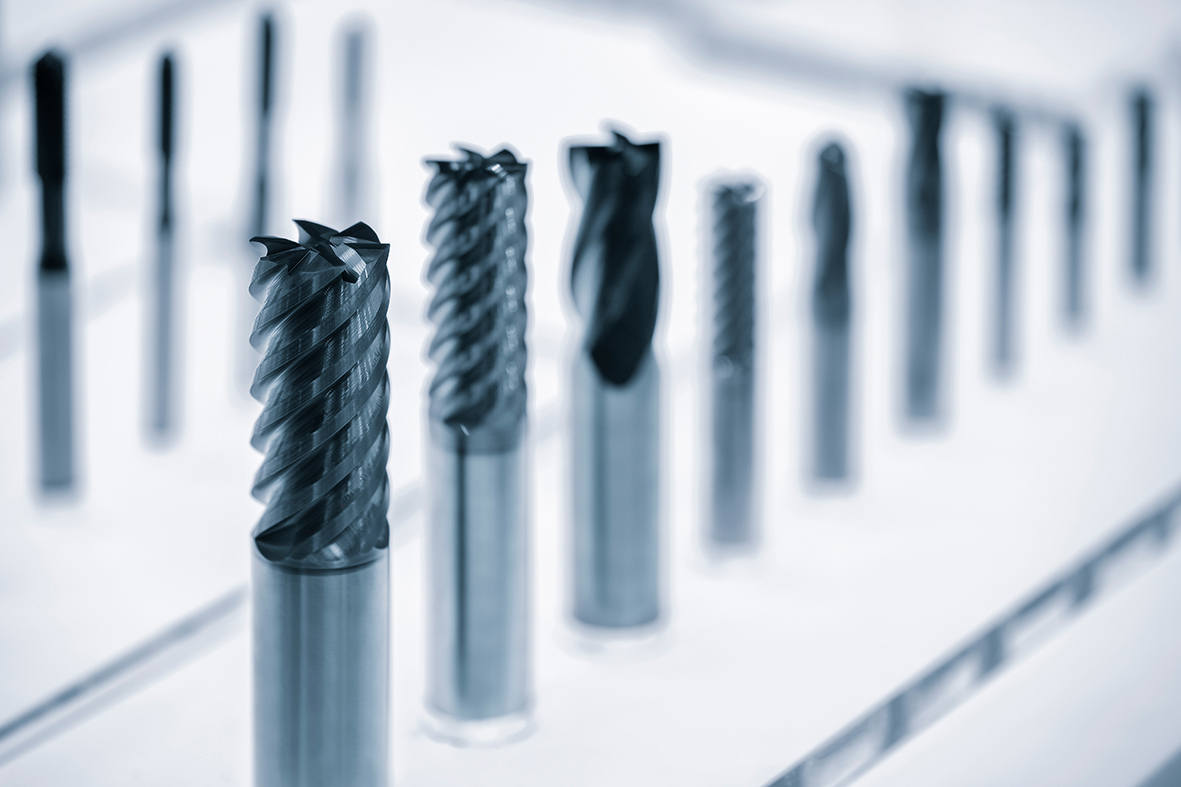
A milling cutter is a rotary multi-tooth cutting tool used in milling operations. Each tooth removes material intermittently, allowing the cutter to machine surfaces such as flats, steps, grooves, and complex contours. In CNC machining, the milling cutter plays a central role. CNC milling, controlled by computer programs, allows for automated, high-precision machining of complex parts. The right milling cutter directly affects the quality, accuracy, and efficiency of the machining process.
Common Types of Milling Cutters
There are many types of milling cutters, each suited to specific tasks. Below is a comparison of the most commonly used milling tools:
Milling cutter type | Features | Typical Uses |
End Mills (End Mill) | The tool is cylindrical, with the cutting edges distributed on the circumference and end face of the tool bar, and can cut in the axial and radial directions. Coarse-tooth end mills have fewer cutting edges, higher strength, and larger chip evacuation space, making them suitable for removing large amounts of material; fine-tooth end mills are suitable for fine machining. | Used for general cutting such as plane processing, step and groove processing on general milling machines. |
Ball milling cutter (Ball end milling cutter) | The tool tip is spherical and can process contoured surfaces and 3D shapes. Ball nose end mills are made of round cutting edges and are particularly suitable for machining complex shapes such as mold surfaces and curved contours. | Commonly used for three-dimensional surface milling, mold cavity or surface detail processing. |
Rough milling cutter (Roughing tool) | Also known as "pig milling cutter", the tooth shape is specially designed to resist vibration. It can quickly remove a large amount of metal during heavy cutting, but the surface roughness is relatively high. | It is suitable for rough machining stage, such as large-scale material removal milling, steel parts reserved material removal, etc. |
Face milling cutter | The cutting edges are located on the end face and the circumference, so a large area can be processed at one time. Commonly used for large surface cutting on vertical or gantry milling machines. The cutter body structure includes integral, toothed or indexable types, and multiple cutting edges can improve processing efficiency. | Used for machining large flat surfaces and end faces, it can quickly achieve efficient flat cutting. |
Comparison of Milling Cutter Materials and Coatings
Common materials and coatings of milling cutters determine their performance and scope of application:
- High Speed Steel (HSS): Good toughness, good wear resistance and low cost, suitable for cutting of general steel and non-ferrous metals. For harder materials such as stainless steel, high-speed steel with added vanadium and cobalt can be used to improve wear resistance and toughness.
- Cemented Carbide: High hardness and excellent heat resistance, but slightly low toughness. Carbide tools have excellent rigidity and can be used for a long time when cutting difficult-to-cut materials (such as cast iron, alloy steel, aluminum alloy, etc.) at high speeds. The cutting rate is about 2-3 times that of HSS. Carbide tools can significantly improve tool life and cutting stability.
- Tool coating: Surface coating can further improve wear resistance and heat resistance. Common coatings include titanium nitride (TiN), titanium boron nitride (TiCN), etc. NewTiAlNThe coating has higher hardness, higher oxidation temperature, excellent hot hardness, strong adhesion and low friction coefficient. It is particularly suitable for high-speed cutting of high-alloy steel, stainless steel, titanium alloy and nickel-based alloy and other materials. Compared with traditional TiN, TiAlN has better oxidation resistance at high temperatures, which can significantly extend tool life and improve machining efficiency.
How to Choose the Right Milling Cutter Consider the following:
- Processing materials and applications:Select the tool according to the workpiece material. For hard materials (stainless steel, high-hardness alloy), carbide or cobalt steel milling cutters should be used to resist high temperature and wear; for soft materials (such as aluminum and copper), high-speed steel tools can be used to reduce cutting adhesion. Generally, soft materials such as aluminum alloys tend to use 2-3-edge tools to increase chip evacuation space; hard materials such as steel use 4-edge or more edge tools to improve rigidity. Depending on the roughing or finishing stage, coarse teeth or roughing milling cutters are used for rough cutting to achieve high removal rates, while fine teeth or finishing milling cutters are used for finishing to achieve excellent surface finish.
- Number of cutting edges and geometry:The number of tool edges affects cutting stability and feed efficiency. The more blades there are, the higher the rigidity of the tool is and the greater the feed it can withstand, but the chip removal space is relatively reduced; the fewer blades there are, the stronger the chip removal capability is, which is suitable for scenarios where burrs are prone to occur or a large amount of chip removal is required. According to the processing requirements, the appropriate helix angle and tool tip chamfer can be selected to optimize chip flow and reduce vibration.
- Tool handle and clamping system:Tool holder rigidity and precision are important factors in improving milling performance. It is recommended to use a high-precision tool holder that matches the machine specifications (such as BT, HSK, ISO, etc.).PARFAITEProvidedShrink Fit Chuck,Hydraulic ChuckandHER high speed collet handleThe series of products have high rigidity and high precision clamping capabilities. For example, Puhui's HER collet chuck tool holder adopts a special trapezoidal screw thread design, with a runout of less than 5µm during clamping and a clamping torque that is 2.3 times that of ordinary ER tool holders, which can optimize cutting depth and feed efficiency in heavy cutting; the heat shrink tool holder expands the inner hole through induction heating, which can maintain stable clamping and reduce interference under high-speed milling; the hydraulic tool holder uses hydraulic expansion to achieve a clamping accuracy of 3µm and has a damping and vibration reduction effect, which can effectively reduce cutting chatter and improve production efficiency. The use of the above high-performance toolholders can enable the milling cutter to achieve the best cutting effect.
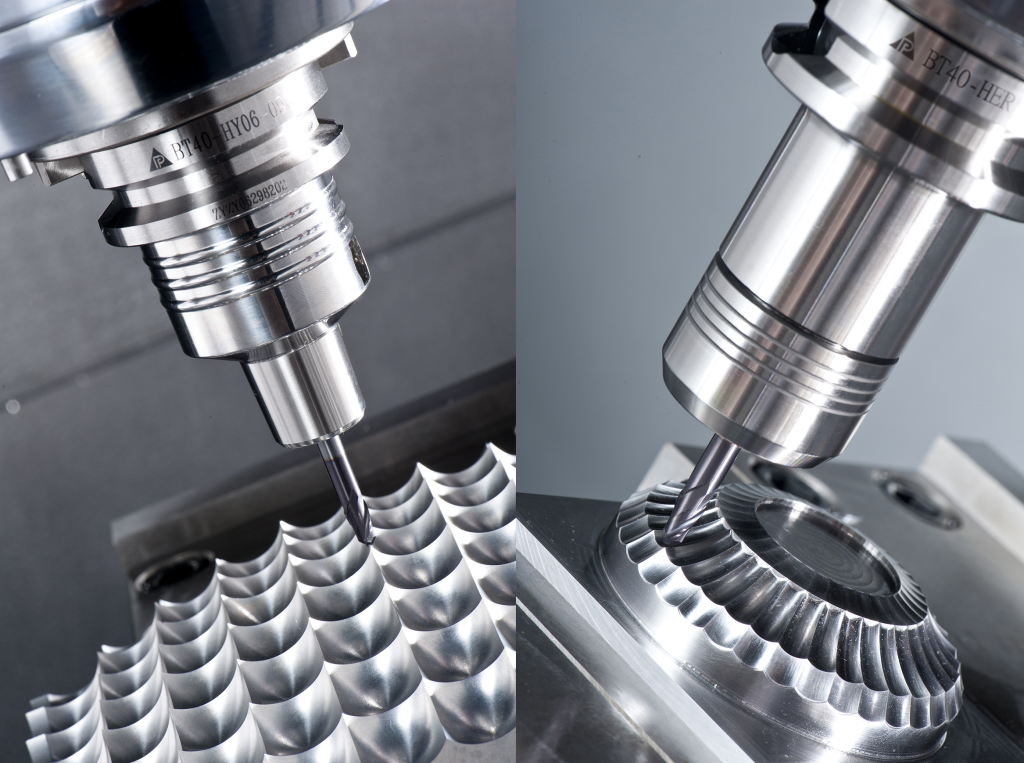
In summary, correctly selecting the milling cutter model and material, and matching it with a high-precision, high-rigidity toolholder, can help improve processing quality and efficiency. Using the right tool and toolholder combination can effectively reduce cutting force, extend tool life and improve workpiece surface roughness. For example, Puhui HER collet chuck can optimize cutting depth and feed efficiency, while hydraulic chuck can significantly reduce cutting vibration and improve production efficiency. It is recommended that readers have a deep understanding of the characteristics of different tools and tool holders according to their processing requirements, and select a qualified combination to achieve stable and efficient CNC milling processing. By properly combining high-performance tools and toolholders, you can significantly improve your machining results and reduce your production costs.
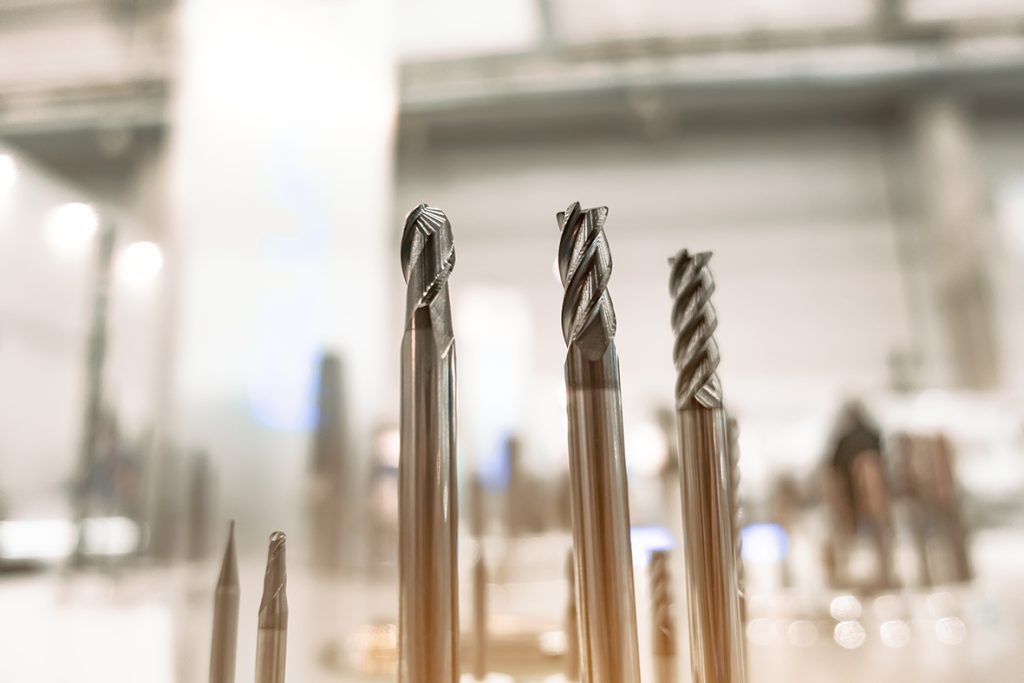